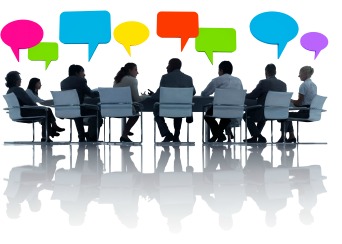
Global supply chain management is a practice that involves the distribution of goods or services throughout a transnational company's network. It aims to maximize profit and minimize waste. There are many methods to improve the efficiency and effectiveness of this process. Software tools can also be developed to monitor it. This article examines the benefits and requirements associated with a degree program in global supply chain administration. The article also discusses the education requirements required for students wishing to pursue this career.
Benefits of a global supply-chain management degree
If you are considering a career with global supply chain managers, a degree is in global logistics management. This program will help you become a leader in your field. Graduates will have advanced knowledge of supply chain management and advanced analytical skills. They will also have a deep understanding of how to optimize the commercial network. You can also get a global supply management degree if you're already employed.
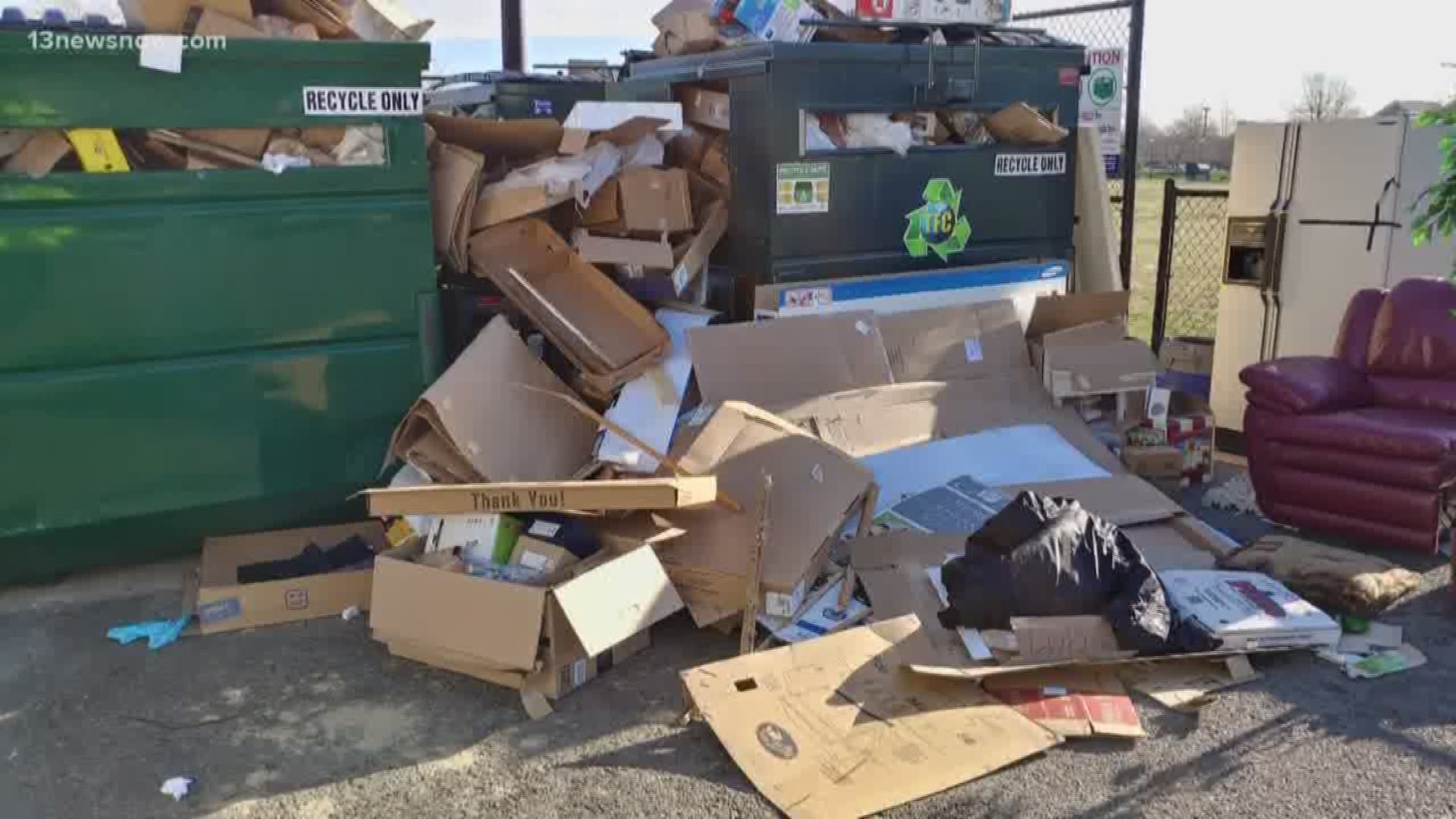
The curriculum will teach you about the intricacies and operations of production, inventory management, warehousing, global supplier relationships, and production planning. In addition, students will learn how to build and maintain strong relationships with suppliers across the globe. Students will complete both practical research and applied coursework, which allows them to gain real-world industry experience. You will be able to work in this industry upon graduation.
Graduates of the program have many career options
The field of global supply chain management includes a number of job opportunities in a variety of industries. Businesses need to manage costs. Graduates in global supply chain management can help businesses make money. You could manage the entire supply chain from a single location to another or travel internationally, depending on the type of job you choose. Career opportunities for a graduate of global supply chain management vary considerably, but these are among the most common.
Knowledge of the supply chain is the most important skill to be successful in this field. Candidates should have a solid understanding of supply chains, and the ability communicate with nontechnical colleagues. A background in the Internet Age will give graduates a unique understanding of retail's effects and enable them to help grow e-retail.
Education requirements
You do not need to have a bachelor's in business administration to be able manage global supply chains. A master's degree is required to manage a global supply network. This degree focuses on innovative technologies and advanced analytical instruments, which will help you improve commercial networks' effectiveness. You can do this degree online. This program will help you to develop and implement strategies that can be used for the benefit of your business.
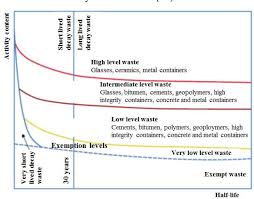
Students who are interested in pursuing a specialization in global supply chain management can also enroll in courses that relate to this field. For example, project management students learn to identify resources, develop budgets, incorporate stakeholder input, and ensure that a project is on track. Students learn to work with international partners and understand the global economic system. Students can choose to take courses in communication and leadership, depending on which program they are enrolled in. Students can also choose to take business communication classes, which will help them improve their communication skills.
FAQ
What are the 3 main management styles?
There are three main management styles: participative, laissez-faire and authoritarian. Each style has its own strengths and weaknesses. Which style do YOU prefer? Why?
Authority - The leader is the one who sets the direction and expects everyone in the organization to follow it. This style works best in large organizations that are stable and well-organized.
Laissez-faire - The leader allows each individual to decide for him/herself. This style works best when an organization is small and dynamic.
Participative - The leader listens to ideas and suggestions from everyone. This is a great style for smaller organizations that value everyone.
Why is it so important for companies that they use project management techniques
To ensure projects run smoothly and meet deadlines, project management techniques are employed.
Because most businesses depend heavily on project work to produce goods or services,
Companies need to manage these projects efficiently and effectively.
Companies could lose their time, reputation, and money without effective project management.
What is the difference between TQM and Six Sigma?
The main difference between these two quality management tools is that six sigma focuses on eliminating defects while total quality management (TQM) focuses on improving processes and reducing costs.
Six Sigma is an approach for continuous improvement. It emphasizes the elimination of defects by using statistical methods such as control charts, p-charts, and Pareto analysis.
The goal of this method is to reduce variation in product output. This is done by identifying and correcting the root causes of problems.
Total quality management involves measuring and monitoring all aspects of the organization. It also involves training employees to improve performance.
It is often used as a strategy to increase productivity.
What is TQM, exactly?
When manufacturing companies realized that price was not enough to compete, the industrial revolution brought about the quality movement. They needed to improve the quality and efficiency of their products if they were to be competitive.
In response to this need for improvement, management developed Total Quality Management (TQM), which focused on improving all aspects of an organization's performance. It involved continuous improvement, employee participation, and customer satisfaction.
How do we build a culture that is successful in our company?
A culture of respect and value within a company is key to a productive culture.
It's founded on three principal principles:
-
Everybody can contribute something valuable
-
People are treated fairly
-
Respect is shared between individuals and groups
These values are reflected in the way people behave. They will treat others with kindness and consideration.
They will respect the opinions of others.
They can also be a source of inspiration for others.
In addition, the company culture encourages open communication and collaboration.
People are free to speak out without fear of reprisal.
They know that they will not be judged if they make mistakes, as long as the matter is dealt with honestly.
Finally, the company culture encourages honesty as well as integrity.
Everyone knows that they must always tell the truth.
Everyone knows that there are rules and regulations that apply to them.
People don't expect special treatment or favors.
What role can a manager fill in a company’s management?
There are many roles that a manager can play in different industries.
A manager is generally responsible for overseeing the day to day operations of a company.
He/she is responsible for ensuring that the company meets all its financial obligations and produces the goods or services customers want.
He/she is responsible for ensuring that employees comply with all regulations and follow quality standards.
He/she oversees marketing campaigns and plans new products.
Statistics
- This field is expected to grow about 7% by 2028, a bit faster than the national average for job growth. (wgu.edu)
- As of 2020, personal bankers or tellers make an average of $32,620 per year, according to the BLS. (wgu.edu)
- Hire the top business lawyers and save up to 60% on legal fees (upcounsel.com)
- The profession is expected to grow 7% by 2028, a bit faster than the national average. (wgu.edu)
- The BLS says that financial services jobs like banking are expected to grow 4% by 2030, about as fast as the national average. (wgu.edu)
External Links
How To
How can you use the Kaizen method?
Kaizen means continuous improvement. This term was first used by Toyota Motor Corporation in the 1950s. It refers to the Japanese philosophy that emphasizes continuous improvement through small incremental changes. It's a team effort to continuously improve processes.
Kaizen is one the most important methods of Lean Manufacturing. The concept involves employees responsible for manufacturing identifying problems and trying to fix them before they become serious issues. This is how you can improve the quality and lower the cost.
The main idea behind kaizen is to make every worker aware of what happens around him/her. It is important to correct any problems immediately if they are discovered. If someone spots a problem while at work, they should immediately report it to their manager.
Kaizen follows a set of principles. The end product is always our starting point and we work toward the beginning. To improve our factory, for example, we need to fix the machines that produce the final product. Next, we repair the machines that make components. Then, the machines that make raw materials. Then we fix the workers, who directly work with these machines.
This method is known as kaizen because it focuses upon improving every aspect of the process step by step. Once the factory is fixed, we return to the original site and work our way back until we get there.
It is important to understand how to measure the effectiveness and implementation of kaizen in your company. There are several ways to determine whether kaizen is working well. One method is to inspect the finished products for defects. Another method is to determine how much productivity has improved since the implementation of kaizen.
To determine if kaizen is effective, you should ask yourself why you chose to implement kaizen. Did you do it because it was legal or to save money? It was a way to save money or help you succeed.
Suppose you answered yes to any of these questions, congratulations! You're now ready to get started with kaizen.