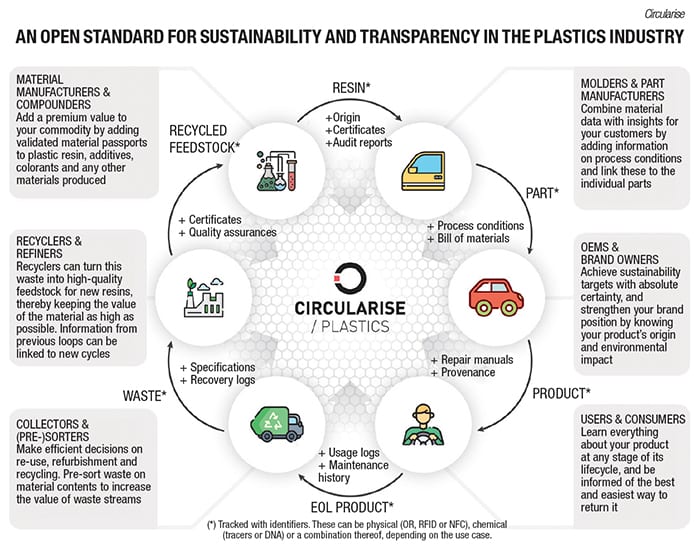
Process safety management is a disciplined approach to the management of the integrity of processes and operating systems in a facility. This system must be up-to-date at least five years after it is established. Process safety management aims to prevent accidents. These steps will help you get started with process management. These steps will help ensure your facility is as safe as it can be and to prevent accidents.
Process safety management can be described as a disciplined framework that manages the integrity of operating system and process processes.
Process safety management aims to lower the risk of accidents and increase productivity. It helps to reduce risks within the plant as well as inherently safer equipment. It requires strict adherence to operating procedures, hazard assessment, and rigorous compliance with all regulations. It includes training and maintenance, along with process control. It is an integral part of any safety-conscious organization.
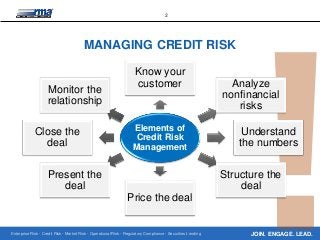
It should be updated at least every 5 years
OSHA's Occupational Safety and Health Administration (OSHA), requires that processes are regularly reviewed and revised. This includes the development and updating of safety procedures and processes. All employees should have access to the information. Written investigation reports and procedures should be retained for five years. Employees should have easy access to up-to-date process safety information. To help employers meet their needs, they can turn to safety risk management experts.
It is a legal requirement to have major hazard equipment.
All major hazards facilities must have a process safety management system. Employers must also develop and implement the program. Most cases, the plan will include a safety alarm to alert employees to evacuate. It should also contain emergency procedures to aid employees who are not physically able to evacuate the hazardous zone.
It prevents incidents
A well-designed safety management system will improve the company's profitability, safety performance and quality. It can also enhance the company's environmental accountability. It can also help reduce incidents. These are all vital areas to ensure the company's long-term success. Below is a list of benefits that a process safety management program can bring to a company. It can help a company prevent injuries and enhance the safety of its customers and employees.
It is time-consuming.
Implementing process safety management in a hazardous chemical facility can be a complex and time-consuming task. Even if OSHA doesn't regulate process safety management programs, it does require facilities to have a written plan for implementation and to meet 14 minimum requirements. To collect data, compile risk assessments and other information, some companies rely on spreadsheets or forms. This is time-consuming and there is the possibility of human error.
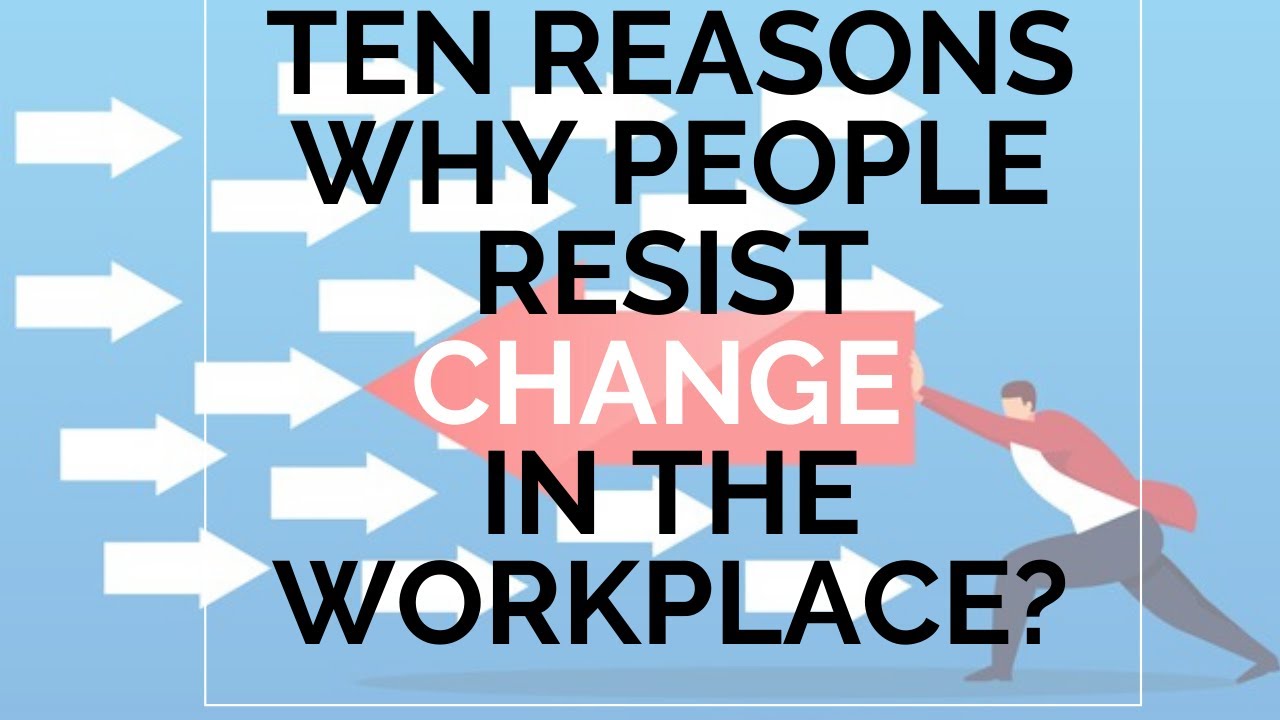
It involves employee participation
Pennsylvania State University has adopted a PSM program with an Employee Participation component. This element leverages employees' knowledge, experience, and unique perspectives to improve safety. The program provides information about the different participation mechanisms and minimum requirements. It is crucial to involve all employees in process safety management and include them in all aspects. To prevent serious incidents, employees must be involved in PSM. But, how do you ensure that all employees are engaged in the program?
FAQ
What is TQM, exactly?
The quality movement was born during the industrial revolution when manufacturing companies realized they could not compete on price alone. If they wanted to stay competitive, they needed to improve their quality and efficiency.
In response to this need for improvement, management developed Total Quality Management (TQM), which focused on improving all aspects of an organization's performance. It included continuous improvement, employee involvement and customer satisfaction.
What are management concepts?
Management Concepts are the principles and practices managers use to manage people and resources. These topics include job descriptions, performance evaluations and training programs. They also cover human resource policies, job description, job descriptions, job descriptions, employee motivation, compensation systems, organizational structures, and many other topics.
What is the difference in a project and program?
A program is permanent, whereas a project is temporary.
A project is usually defined by a clear goal and a set deadline.
It is often carried out by a team of people who report back to someone else.
A program usually has a set of goals and objectives.
It is often implemented by one person.
How does a manager motivate their employees?
Motivation refers to the desire or need to succeed.
It is possible to be motivated by doing something you enjoy.
Another way to get motivated is to see yourself as a contributor to the success of the company.
For example, if your goal is to become a physician, you will probably find it more motivational to see patients rather than to read a lot of medicine books.
Another type of motivation comes from within.
Perhaps you have a strong sense to give back, for example.
Perhaps you enjoy working hard.
Ask yourself why you feel so motivated.
You can then think of ways to improve your motivation.
What does "project management" mean?
Management is the act of managing activities in order to complete a project.
This includes defining the scope, identifying the requirements and preparing the budget. We also organize the project team, schedule the work, monitor progress, evaluate results, and close the project.
What are the three main management styles you can use?
These are the three most common management styles: participative (authoritarian), laissez-faire (leavez-faire), and authoritarian. Each style has its own strengths and weaknesses. Which style do yo prefer? Why?
Authoritarian – The leader sets a direction and expects everyone follows it. This style works best if the organization is large and stable.
Laissez-faire: The leader lets each person decide for themselves. This approach works best in small, dynamic organizations.
Participative - Leaders listen to all ideas and suggestions. This style works best in smaller organizations where everyone feels valued.
Statistics
- The profession is expected to grow 7% by 2028, a bit faster than the national average. (wgu.edu)
- The average salary for financial advisors in 2021 is around $60,000 per year, with the top 10% of the profession making more than $111,000 per year. (wgu.edu)
- Hire the top business lawyers and save up to 60% on legal fees (upcounsel.com)
- The BLS says that financial services jobs like banking are expected to grow 4% by 2030, about as fast as the national average. (wgu.edu)
- UpCounsel accepts only the top 5 percent of lawyers on its site. (upcounsel.com)
External Links
How To
How do I get my Six Sigma license?
Six Sigma is a tool for quality management to improve processes and increase efficiency. It's a system that allows companies to get consistent results from operations. The name is derived from the Greek word "sigmas", which means "six". Motorola developed this process in 1986. Motorola realized that it was important to standardize manufacturing processes so they could produce products quicker and cheaper. They had been having problems with consistency because of the many different people who were doing the work. To resolve this issue, they used statistical tools like Pareto analysis and control charts. Then they would apply the techniques to all parts of the operation. This technique would enable them to make improvements in areas that needed it. When you are trying to obtain your Six Sigma certification, there are three steps. First, you need to determine if your qualifications are valid. You will need classes to pass before you can begin taking tests. After you have passed the classes, you can start taking the exams. You'll need to go back and review all the information you received in class. Then, you'll be ready to take the test. If you pass, you'll get certified. Final, your certifications can be added to you resume.