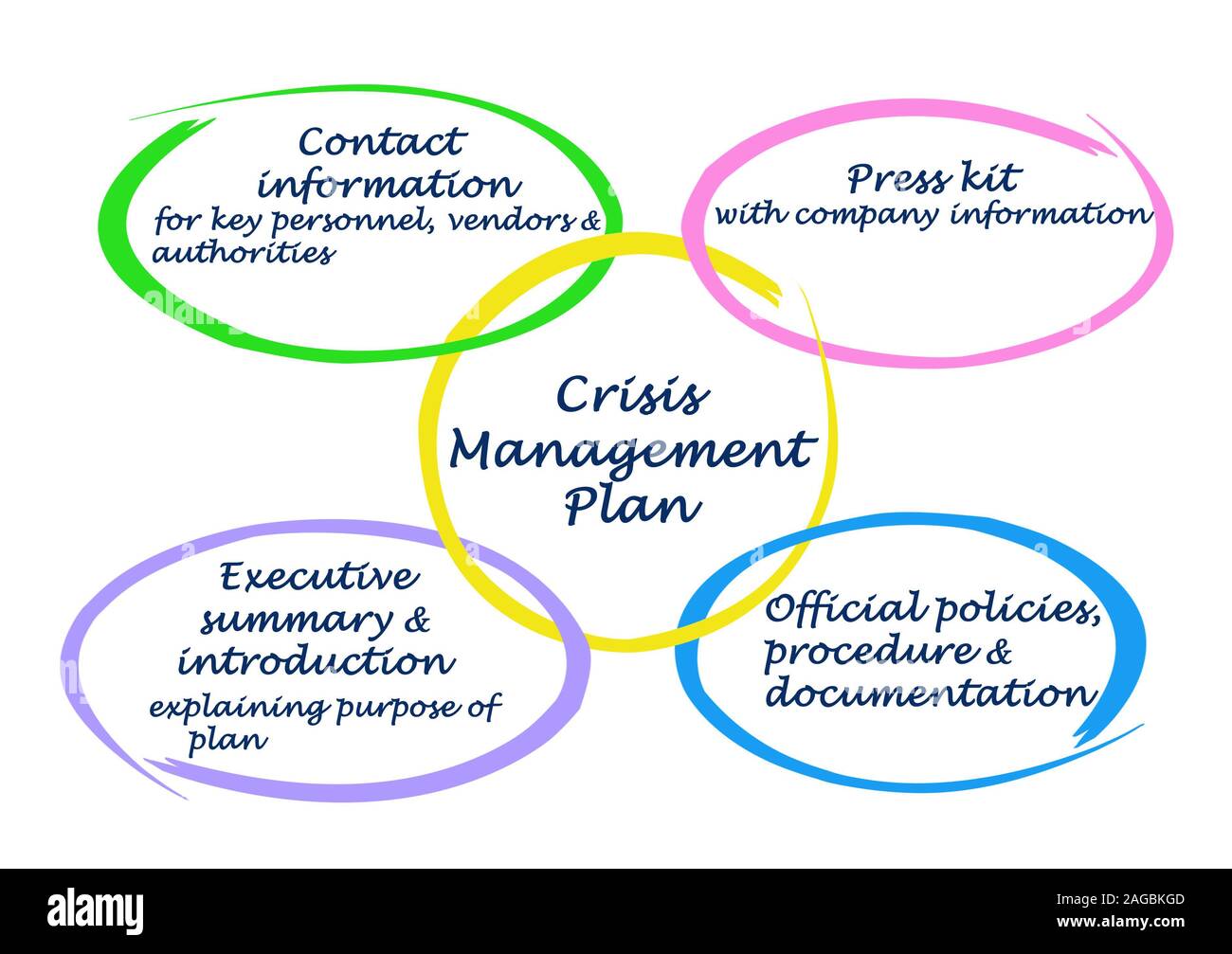
Cyber risk is any type risk that involves information technology. Information technology risks range from data breaches to access risks. These risks concern both business and private data and need to be properly managed. This article will provide you with information on the various risks associated with IT. It will also help guide you in choosing the best measures to protect your business.
Information technology risk
Cyber risk is also known as information technology risk. It refers to any risk that involves information technology. This type of risk is the most prevalent among small businesses and startups, but larger companies must also consider information technology risks to ensure business continuity. There are ways that businesses can mitigate cyber attack risks and protect themselves from the potential negative impacts on their bottom line.
It is essential to have a holistic and systematic approach when managing information technology risks. This includes systematic risk analysis and systemic risk management processes. This includes decision-makers willing to reverse prior decisions, a well-defined communications structure, and strong risk-taking.
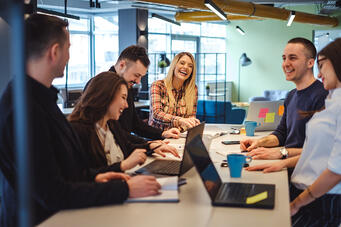
Data breach risk
Unauthorized persons can steal, access, or modify data from a computer system. This can lead to financial loss and reputational damage as well as lawsuits. It can also compromise the security of a government agency's systems. Furthermore, breaches can result in highly sensitive information being exposed. An attacker might be able to compromise government IT infrastructures and gain access trade secrets. Private data can also be sold on darknet marketplaces or used by third parties to create fraudulent accounts.
IT risks such as data breaches can be serious and companies should immediately notify their customers and employees. The plan should remain current and be regularly updated.
Access risk
IT security must address the concern of access risk. This is the threat of unauthorized access being made to vital information. Access can occur from both logical or physical access. Accessing sensitive information can be done via physical access. This network connects users to these systems. This network allows employees to gain unauthorised access and control over confidential or proprietary data.
It can be difficult to manage access permissions. It can be difficult to assign the right permissions to users to many different systems and applications. This risk can be minimized by limiting access to certain types users within organizations.
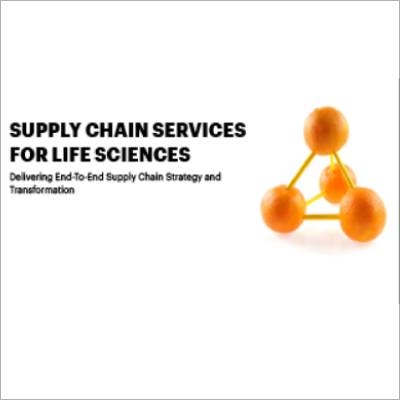
Control measures
To reduce IT risks, you have many options. IT security can be reduced by training staff, providing equipment and implementing physical security measures. To reduce risk, all control measures should be combined. You must also use administrative controls such job rotations to limit exposure. Additionally, respirators as well as PPE (goggles and respirators) are necessary. These measures should work in conjunction with each other and be communicated to employees and reviewed on a regular basis.
The basis of risk control measures should be based upon a risk assessment. In other words, you need to identify the risks that are most significant to your business and determine the best controls. These measures must be cost-effective as well as effective.
Preparation of reactions
Workers must be aware and prepared for any reaction. Workers in categories C or D should only perform tasks that are not associated with undue hazards. Workers in the A category should be careful about potential risks such as carcinogens mutagens, terogens or pyrophoric compounds. Furthermore, workers should be aware of explosion risks.
FAQ
What are the 3 basic management styles?
There are three types of management: participative, laissez faire, and authoritarian. Each style has strengths and flaws. Which style do YOU prefer? Why?
Autoritarian - The leader sets direction and expects everyone else to follow it. This style is best when the organization has a large and stable workforce.
Laissez-faire - The leader allows each individual to decide for him/herself. This approach works best in small, dynamic organizations.
Participative – The leader listens and takes in ideas from all. This style works best in smaller organizations where everyone feels valued.
What is the difference in Six Sigma and TQM?
The main difference between these two quality management tools is that six sigma focuses on eliminating defects while total quality management (TQM) focuses on improving processes and reducing costs.
Six Sigma is a method for continuous improvement. It emphasizes the elimination of defects by using statistical methods such as control charts, p-charts, and Pareto analysis.
The goal of this method is to reduce variation in product output. This is achieved by identifying and addressing the root causes of problems.
Total quality management includes monitoring and measuring all aspects of an organization's performance. It also involves training employees to improve performance.
It is used to increase productivity.
How can we create a culture of success in our company?
A company culture that values and respects its employees is a successful one.
It's based on three main principles:
-
Everyone has something valuable to contribute
-
People are treated fairly
-
There is mutual respect between individuals and groups
These values are reflected by the way people behave. They will treat others with consideration and courtesy.
They will be respectful of the opinions of other people.
They can also be a source of inspiration for others.
In addition, the company culture encourages open communication and collaboration.
People are free to speak out without fear of reprisal.
They know mistakes will be accepted as long as they are dealt with honestly.
Finally, the company culture encourages honesty as well as integrity.
Everyone understands that the truth is always best.
Everyone recognizes that rules and regulations are important to follow.
Nobody expects to be treated differently or given favors.
What are the five management processes?
Each business has five stages: planning, execution and monitoring.
Planning means setting goals for the long-term. It includes defining what you want to achieve and how you plan to do it.
Execution takes place when you actually implement the plans. These plans must be adhered to by everyone.
Monitoring allows you to monitor your progress towards achieving your goals. This should involve regular reviews of performance against targets and budgets.
Review events take place at each year's end. They are a chance to see if everything went smoothly during the year. If not, it is possible to make improvements for next year.
After each year's review, evaluation occurs. It helps identify what worked well and what didn't. It also gives feedback on how well people did.
What are management concepts?
Management concepts are the principles and practices used by managers to manage people, resources. These include topics such as human resource policies and job descriptions, performance assessments, training programs and employee motivation.
What is the difference in leadership and management?
Leadership is about influencing others. Management is about controlling others.
Leaders inspire others, managers direct them.
A leader motivates people to achieve success; a manager keeps workers on task.
A leader develops people; a manager manages people.
What role does a manager play in a company?
Different industries have different roles for managers.
Managers generally oversee the day-today operations of a business.
He/she is responsible for ensuring that the company meets all its financial obligations and produces the goods or services customers want.
He/she is responsible for ensuring that employees comply with all regulations and follow quality standards.
He/she designs new products or services and manages marketing campaigns.
Statistics
- As of 2020, personal bankers or tellers make an average of $32,620 per year, according to the BLS. (wgu.edu)
- Our program is 100% engineered for your success. (online.uc.edu)
- UpCounsel accepts only the top 5 percent of lawyers on its site. (upcounsel.com)
- Hire the top business lawyers and save up to 60% on legal fees (upcounsel.com)
- Your choice in Step 5 may very likely be the same or similar to the alternative you placed at the top of your list at the end of Step 4. (umassd.edu)
External Links
How To
What is Lean Manufacturing?
Lean Manufacturing techniques are used to reduce waste while increasing efficiency by using structured methods. These processes were created by Toyota Motor Corporation, Japan in the 1980s. It was designed to produce high-quality products at lower prices while maintaining their quality. Lean manufacturing emphasizes removing unnecessary steps from the production process. It is composed of five fundamental elements: continuous improvement; pull systems, continuous improvements, just-in–time, kaizen, continuous change, and 5S. Pull systems involve producing only what the customer wants without any extra work. Continuous improvement means continuously improving on existing processes. Just-in-time is when components and other materials are delivered at their destination in a timely manner. Kaizen refers to continuous improvement. It is achieved through small changes that are made continuously. The 5S acronym stands for sort in order, shine standardize and maintain. These five elements can be combined to achieve the best possible results.
Lean Production System
The lean production system is based on six key concepts:
-
Flow is about moving material and information as near as customers can.
-
Value stream mapping - break down each stage of a process into discrete tasks and create a flowchart of the entire process;
-
Five S's: Sort, Shine Standardize, Sustain, Set In Order, Shine and Shine
-
Kanban is a visual system that uses visual cues like stickers, colored tape or stickers to keep track and monitor inventory.
-
Theory of constraints: identify bottlenecks in your process and eliminate them using lean tools, such as kanban board.
-
Just-in Time - Send components and material directly to the point-of-use;
-
Continuous improvement - incremental improvements are made to the process, not a complete overhaul.