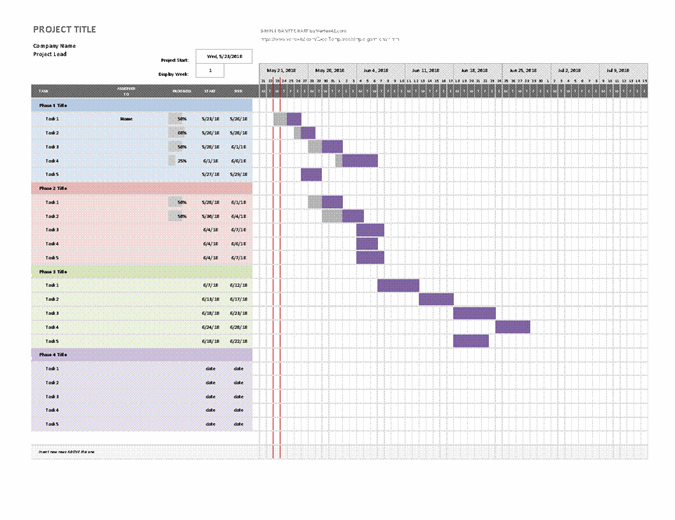
The key tool for quality and risk management is process knowledge management. It is a framework that allows for the linking of past knowledge and current knowledge. It can also be used to support continuous improvement. Let's look at some of the many benefits of process knowledge management. Here are some examples. It might surprise you how valuable it is to your organization. And what's more, it's easy to implement.
Lessons learned
Your company should have a template that outlines the lessons learned. This template should be easily accessible by all employees. If not, it is better to use a document management system to share the lessons with your team. While the template should be easy to understand by your team members, it is worth testing other formats. The more complex your document is, the less likely it will be shared by your employees. It is therefore important to select the best format for your document and engage your employees.
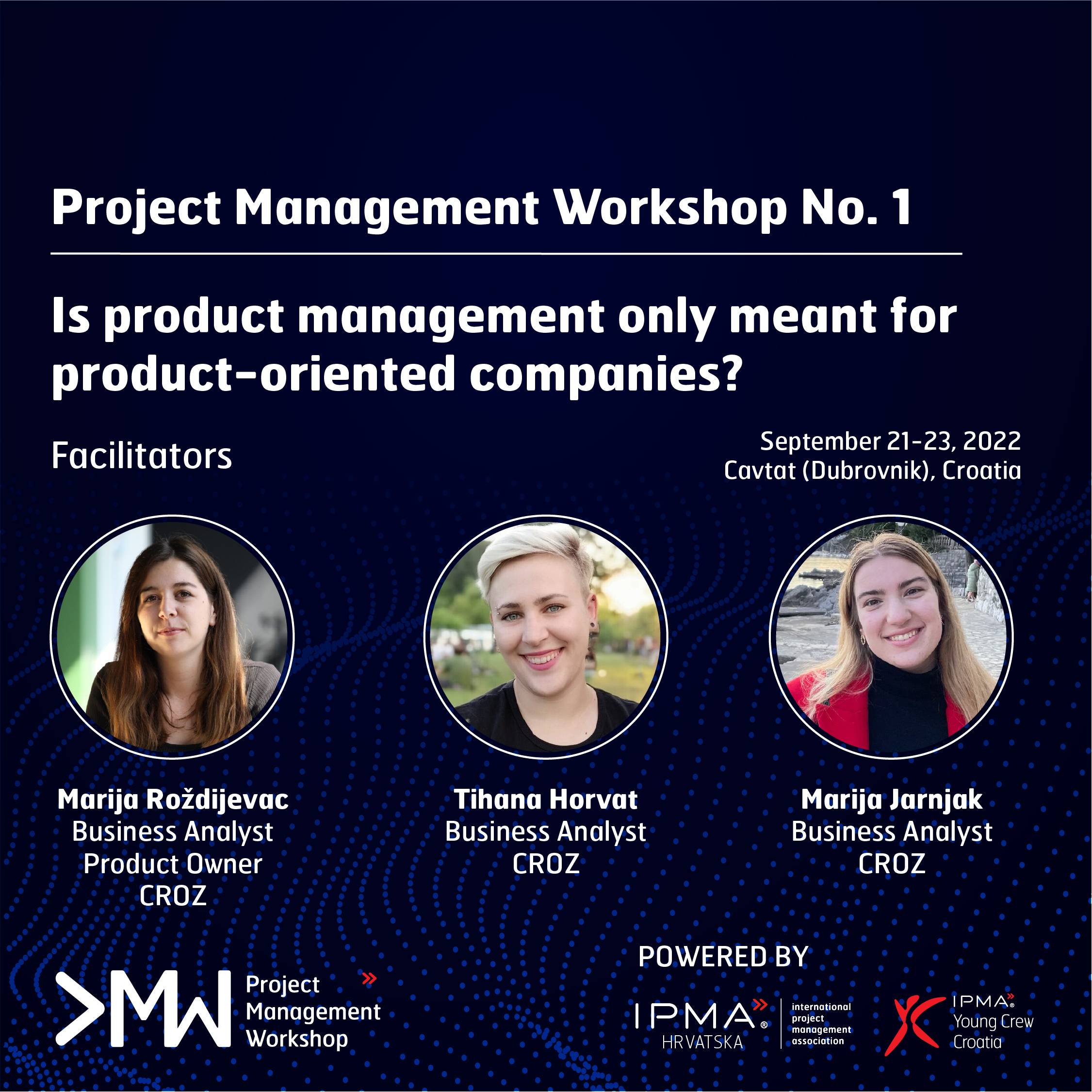
Expertise location
Expert location is now more than biographical data. It allows you to share your knowledge and find the right employees to answer your questions. A majority of people have a LinkedIn or Facebook profile with their area of expertise. These tools help to structure information and give people places to describe their projects as well as publications and knowledge. This can help them build their reputation and increase their visibility.
Communities & Networks
Virtual communities are a way to facilitate cross-industry collaborations and strategic know-management. These communities encourage communication and dissemination to new methods, processes, tools, and approaches that improve performance and innovate in organisations. They can be used to improve the effectiveness of meetings and share case histories. The use of communities in industrial manufacturing has many advantages and is being explored by a number of industry leaders. For more information, see Communities & networks for process knowledge management: A framework for effective knowledge management, communities and networks are designed to bring together groups of people from a variety of disciplines or locations.
Content management
While a content-management system can store a training document with 200 pages of information, it cannot replace a knowledge management system that can capture institutional and user-generated knowledge about a specific topic. Ideally, such a system can capture information from various perspectives, which can be useful for making better decisions and serving customers. For example: If a particular company sells cars then a content-management platform can store all of its sales training materials.
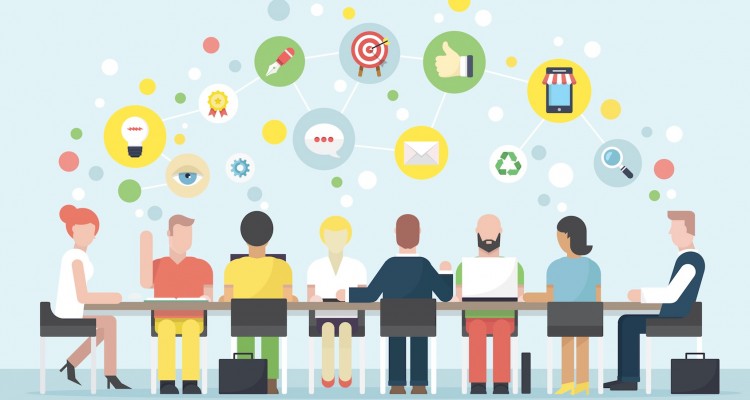
Knowledge mapping
If you're interested in leveraging your knowledge assets to improve your process, knowledge mapping can be a great solution. Knowledge mapping is a powerful method for identifying gaps in knowledge and uncovering them for a better process. It is also an excellent tool for increasing collaboration and engagement among departments. Once you have mapped your knowledge, it is possible to start standardizing processes. Knowledge maps are a great way for your organization to share and disseminate the best practices and improve its processes.
FAQ
How can a manager motivate employees?
Motivation can be defined as the desire to achieve success.
You can get motivated by doing something enjoyable.
Or you can get motivated by seeing yourself making a contribution to the success of the organization.
For example: If you want to be a doctor, you might find it more motivating seeing patients than reading medical books all day.
A different type of motivation comes directly from the inside.
One example is a strong sense that you are responsible for helping others.
Perhaps you enjoy working hard.
If you don't feel motivated, ask yourself why.
Then think about how you can make your life more motivating.
What are the 3 main management styles?
These are the three most common management styles: participative (authoritarian), laissez-faire (leavez-faire), and authoritarian. Each style is unique and has its strengths as well as weaknesses. What style do you prefer? Why?
Autoritarian – The leader sets the direction for everyone and expects them to follow. This style works best if the organization is large and stable.
Laissez-faire – The leader gives each individual the freedom to make decisions for themselves. This style works best when an organization is small and dynamic.
Participative – Leaders are open to suggestions and ideas from everyone. This style is best for small organizations where everyone feels valued.
What is TQM?
The industrial revolution led to the birth and growth of the quality movement. Manufacturing companies realized they couldn't compete solely on price. They needed to improve the quality and efficiency of their products if they were to be competitive.
In response to this need for improvement, management developed Total Quality Management (TQM), which focused on improving all aspects of an organization's performance. It included continuous improvement processes, employee involvement, and customer satisfaction.
What is Six Sigma, exactly?
This is a method of quality improvement that emphasizes customer service, continuous learning, and customer service. This is an approach to quality improvement that uses statistical techniques to eliminate defects.
Motorola created Six Sigma as part of their efforts to improve manufacturing processes in 1986.
The idea spread quickly throughout the industry, and today, many organizations are using six sigma methods to improve product design, production, delivery, and customer service.
What are the four major functions of Management?
Management is responsible to plan, organize, direct, and control people and resources. It includes creating policies and procedures, as well setting goals.
Management assists an organization in achieving its goals by providing direction, coordination and control, leadership, motivation, supervision and training, as well as evaluation.
Management's four main functions are:
Planning - Planning refers to deciding what is needed.
Organizing: Organizing refers to deciding how things should work.
Directing - Directing means getting people to follow instructions.
Controlling – This refers to ensuring that tasks are carried out according to plan.
It can sometimes seem difficult to make business decisions.
Complex business systems have many moving parts. They require people to manage multiple priorities and deal with uncertainty and complexity.
It is important to understand the effects of these factors on the system in order to make informed decisions.
You need to be clear about the roles and responsibilities of each system. Then, you need to think about how these pieces interact with one another.
You need to ask yourself if your previous actions have led you to make unfounded assumptions. You might consider revisiting them if they are not.
You can always ask someone for help if you still have questions after all of this. They might see things differently than you and may have some insights that could help find a solution.
How does a manager develop his/her management skills?
By practicing good management skills at all times.
Managers must continuously monitor the performance levels of their subordinates.
You must act quickly if you notice that your subordinate isn’t performing to their standards.
You must be able to spot what is lacking and how you can improve it.
Statistics
- This field is expected to grow about 7% by 2028, a bit faster than the national average for job growth. (wgu.edu)
- Your choice in Step 5 may very likely be the same or similar to the alternative you placed at the top of your list at the end of Step 4. (umassd.edu)
- The profession is expected to grow 7% by 2028, a bit faster than the national average. (wgu.edu)
- The BLS says that financial services jobs like banking are expected to grow 4% by 2030, about as fast as the national average. (wgu.edu)
- 100% of the courses are offered online, and no campus visits are required — a big time-saver for you. (online.uc.edu)
External Links
How To
How can you use the Kaizen method?
Kaizen means continuous improvement. The term was coined in the 1950s at Toyota Motor Corporation and refers to the Japanese philosophy emphasizing constant improvement through small incremental changes. It's a process where people work together to improve their processes continuously.
Kaizen is one the most important methods of Lean Manufacturing. In this concept, employees who are responsible for the production line must identify problems that exist during the manufacturing process and try to solve them before they become big issues. This improves the quality of products, while reducing the cost.
The main idea behind kaizen is to make every worker aware of what happens around him/her. Correct any errors immediately to avoid future problems. So, if someone notices a problem while working, he/she should report it to his/her manager.
There are some basic principles that we follow when doing kaizen. The end product is always our starting point and we work toward the beginning. For example, if we want to improve our factory, we first fix the machines that produce the final product. We then fix the machines producing components, and the machines producing raw materials. Then, we fix those who work directly with the machines.
This approach is called 'kaizen' because it focuses on improving everything steps by step. When we are done fixing the whole factory, we go back to the beginning and continue until we reach perfection.
To implement kaizen in your business, you need to find out how to measure its effectiveness. There are several ways that you can tell if your kaizen system is working. One of these ways is to check the number of defects found on the finished products. Another method is to determine how much productivity has improved since the implementation of kaizen.
A good way to determine whether kaizen has been implemented is to ask why. Is it because the law required it or because you want to save money. You really believed it would make you successful?
Suppose you answered yes to any of these questions, congratulations! You're ready to start kaizen.