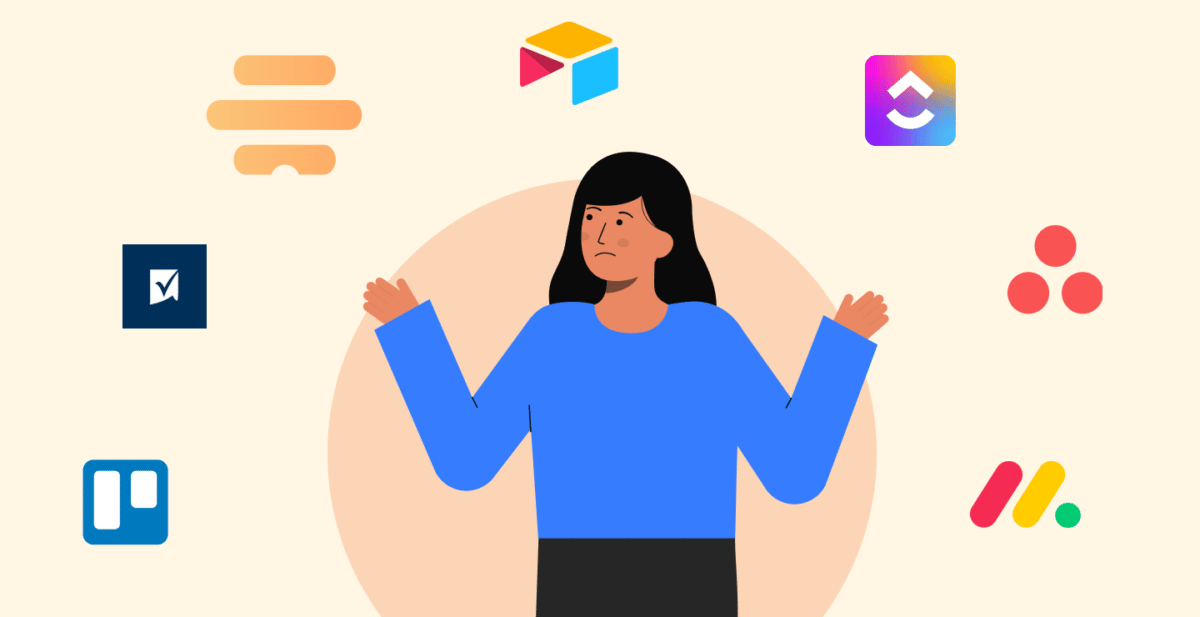
Price risk refers to the possibility that an asset's value will decrease over time. This can happen with any financial instrument, commodity or foreign exchange position. Hedge funds tend to use a more broad definition of price risk due to the many market factors that can cause the price of a particular asset to decrease. Hedging is crucial as it can make the difference in a successful investment or a disaster.
Make investments
When you invest, it is important to take into account price risk. Stocks, equities and commodities can have their prices fluctuate over time. Investors could lose all, or part, of their investment as a result of this fluctuation. Market trends and changes can also cause share prices fluctuations. This risk, which is often overlooked, is vital to investing.
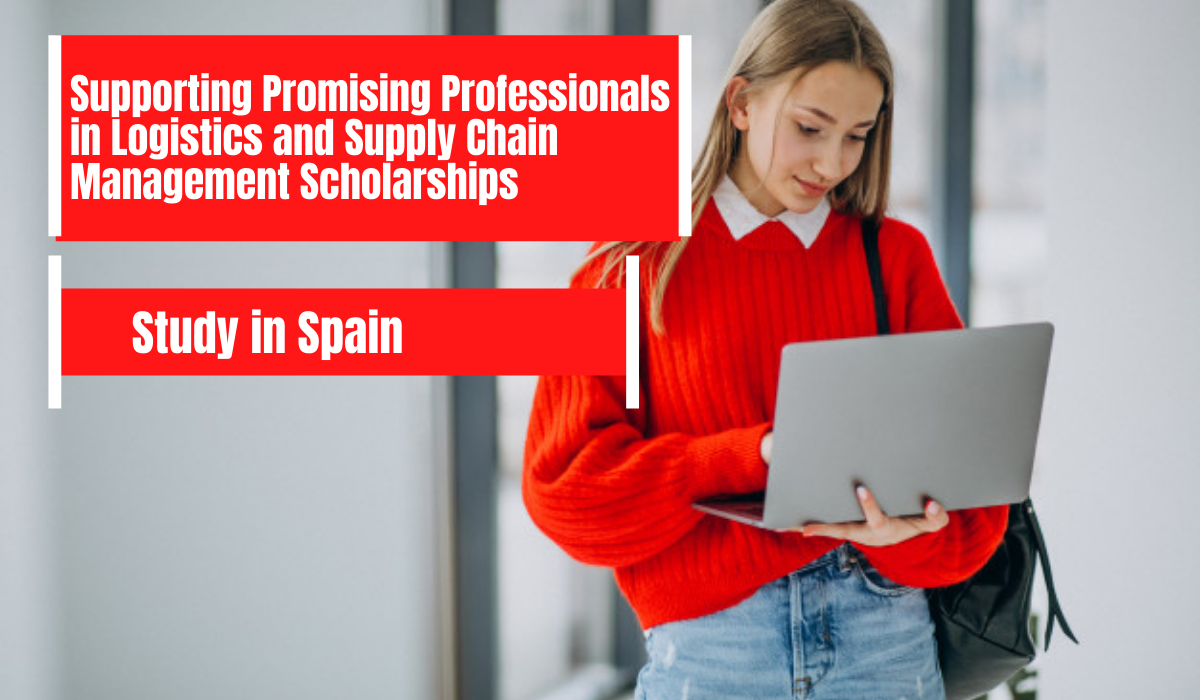
Commodities
As with any investment, there are certain risks associated with the price of a commodity. One such risk is the volatility of price movements, which may be higher than that of other assets. For example, metal prices may move up to 30%. This makes the price risk associated with commodities more complex than with other financial assets.
Foreign exchange
The volatility of the currency markets is a result of a wide range factors. The COVID-19 pandemic, Brexit and the U.S.-China Trade War are just a few of the factors that have caused volatility in the currency market. This volatility is a remarkable shift in the developed markets that had previously been relatively stable during periods when there was calm and quiet.
Financial instruments
This book is designed to help students understand price risk in financial instruments. This includes options and futures contracts. These contracts require the parties to take a specific action. A futures contract would require the buyer to purchase the underlying asset. Option gives the buyer the opportunity to buy or trade a security.
Leverage
Both individuals as well as companies often use leverage when investing. It can be used in many ways, from launching a new business to increasing shareholder value. You can also use it for a home purchase or college education. But, it is crucial to understand how it should be used.
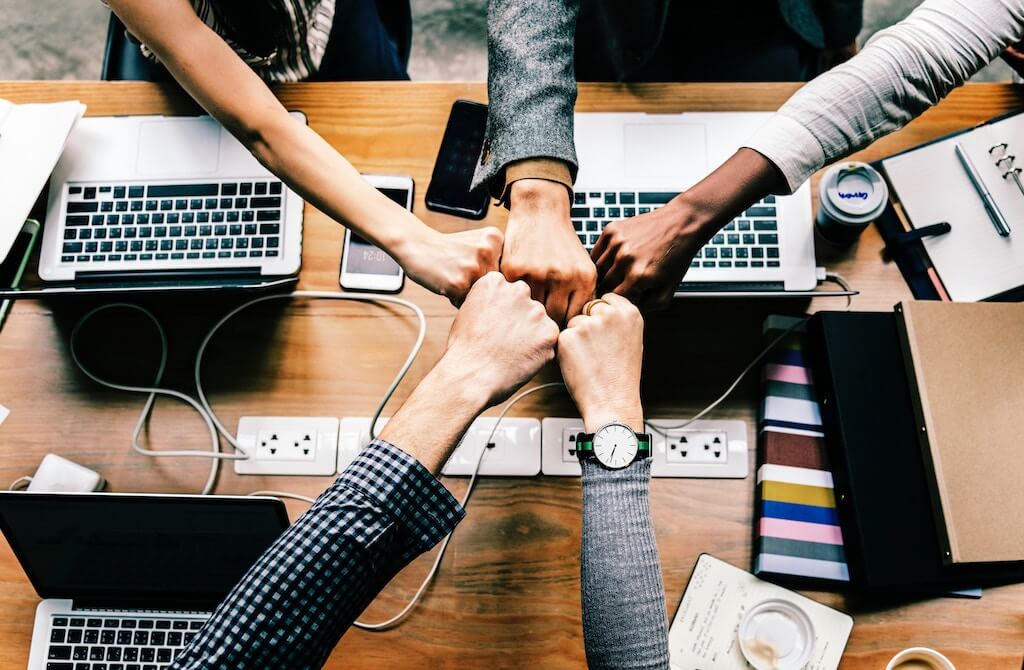
Hedging
This strategy can be used by businesses to hedge against price volatility. This can be done using a variety of financial instruments. It can be used in almost all areas of the business. A manufacturing company selling its products overseas would use hedging to protect against currency fluctuations. Hedging has its costs.
FAQ
What are the five management steps?
These five stages are: planning, execution monitoring, review and evaluation.
Planning involves setting goals for the future. It involves setting goals and making plans.
Execution occurs when you actually carry out the plans. It is important to ensure that everyone follows the plans.
Monitoring is the act of monitoring your progress towards achieving your targets. This should involve regular reviews of performance against targets and budgets.
Reviews take place at the end of each year. These reviews allow you to evaluate whether the year was successful. If not, then it may be possible to make adjustments in order to improve performance next time.
After the annual review, evaluation takes place. It helps to determine what worked and what didn’t. It also gives feedback on how well people did.
What is Six Sigma?
This is a method of quality improvement that emphasizes customer service, continuous learning, and customer service. The goal is to eliminate defects by using statistical techniques.
Motorola created Six Sigma as part of their efforts to improve manufacturing processes in 1986.
The idea quickly spread in the industry. Many organizations today use six-sigma methods to improve product design and production, delivery and customer service.
What are some of the common mistakes made by managers?
Managers sometimes make their own job harder than necessary.
They might not give enough support and delegate the right responsibilities to their staff.
Managers often lack the communication skills necessary to motivate and guide their teams.
Some managers create unrealistic expectations for their teams.
Managers may prefer to solve every problem for themselves than to delegate responsibility.
What kind people use Six Sigma?
Six sigma is a common concept for people who have worked in statistics or operations research. But anyone can benefit from it.
This requires a lot of dedication, so only people with great leadership skills can make the effort to implement it.
What are the 3 main management styles?
The three basic management styles are: authoritarian, laissez-faire, and participative. Each style has strengths and flaws. Which style do your prefer? Why?
Authoritarian – The leader sets a direction and expects everyone follows it. This style works best in large organizations that are stable and well-organized.
Laissez-faire – The leader gives each individual the freedom to make decisions for themselves. This style works best when the organization is small and dynamic.
Participative - The leader listens to ideas and suggestions from everyone. This style is most effective in smaller organizations, where everyone feels valued.
Why is it so important for companies that they use project management techniques
Project management techniques are used to ensure that projects run smoothly and meet deadlines.
This is because most businesses rely heavily on project work to produce goods and services.
These projects must be managed efficiently and effectively by companies.
Companies could lose their time, reputation, and money without effective project management.
What are management theories?
Management concepts are the practices and principles managers use to manage people or resources. They include such topics as human resource policies, job descriptions, performance evaluations, training programs, employee motivation, compensation systems, organizational structure, and many others.
Statistics
- Our program is 100% engineered for your success. (online.uc.edu)
- UpCounsel accepts only the top 5 percent of lawyers on its site. (upcounsel.com)
- As of 2020, personal bankers or tellers make an average of $32,620 per year, according to the BLS. (wgu.edu)
- 100% of the courses are offered online, and no campus visits are required — a big time-saver for you. (online.uc.edu)
- The average salary for financial advisors in 2021 is around $60,000 per year, with the top 10% of the profession making more than $111,000 per year. (wgu.edu)
External Links
How To
How can Lean Manufacturing be done?
Lean Manufacturing techniques are used to reduce waste while increasing efficiency by using structured methods. They were developed in Japan by Toyota Motor Corporation (in the 1980s). The main goal was to produce products at lower costs while maintaining quality. Lean manufacturing focuses on eliminating unnecessary steps and activities from the production process. It is made up of five elements: continuous improvement, continuous improvement, just in-time, continuous change, and 5S. Pull systems allow customers to get exactly what they want without having to do extra work. Continuous improvement refers to continuously improving existing processes. Just-intime refers the time components and materials arrive at the exact place where they are needed. Kaizen refers to continuous improvement. It is achieved through small changes that are made continuously. The 5S acronym stands for sort in order, shine standardize and maintain. These five elements are used together to ensure the best possible results.
Lean Production System
Six key concepts underlie the lean production system.
-
Flow - focus on moving material and information as close to customers as possible;
-
Value stream mapping - Break down each stage in a process into distinct tasks and create an overview of the whole process.
-
Five S's: Sort, Shine Standardize, Sustain, Set In Order, Shine and Shine
-
Kanban - use visual signals such as colored tape, stickers, or other visual cues to keep track of inventory;
-
Theory of constraints - identify bottlenecks in the process and eliminate them using lean tools like kanban boards;
-
Just-in-time - deliver components and materials directly to the point of use;
-
Continuous improvement - Make incremental improvements rather than overhauling the entire process.