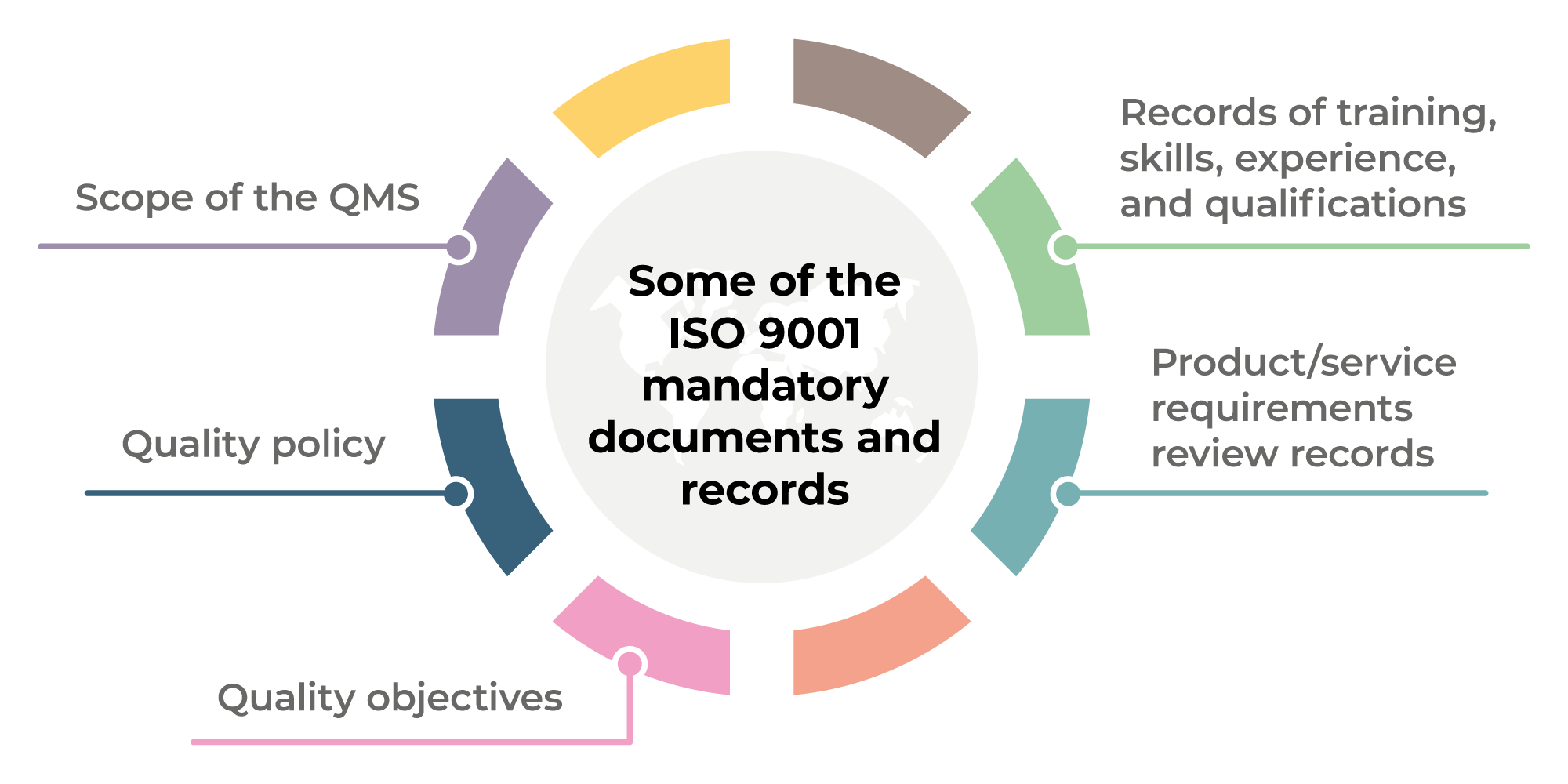
What does management of change mean? The management of change involves a methodical approach to managing the changes. This includes supporting change, preparing for it, and helping people, groups, and organizations deal with it. The term "change" refers to disruptive changes that can affect the day-to-day operations of a company. It can also be a multidisciplinary field, which includes many disciplines. Continue reading to learn more. This article will give you an overview of the term.
Change management can be described as a systematic approach to managing the effects of changes.
It is vital to manage change when individuals or groups face major change. Some people mistakenly think change management is just a plan for communication. However, it is far more complicated than that. Change management requires the ability to adopt corporate strategies, processes, or procedures and lead people through major change. The goal of change management is to reduce negative effects and increase the chances of success by implementing new products, processes, and technologies.
It measures the progress of a particular change
Measurement is an important element of change management. All organizational change initiatives and structured change initiatives include measurement. For example, a project's success can be measured by whether it meets its goals on time and within budget. The progress of a project is not measured in terms it benefits, but change management practitioners are more likely to do this. Instead, they assess participants' performance in change management.
It can disrupt normal operations
Disruption is part of everyday life. It is a reality that organizations are constantly facing. It is important that leaders plan for the change and then implement it in a way that maximizes its benefits. Managers need to assess the potential effects and assess their company's capabilities and resources. These resources include information, product design and brand, as well as inter-departmental relationships and public relations.
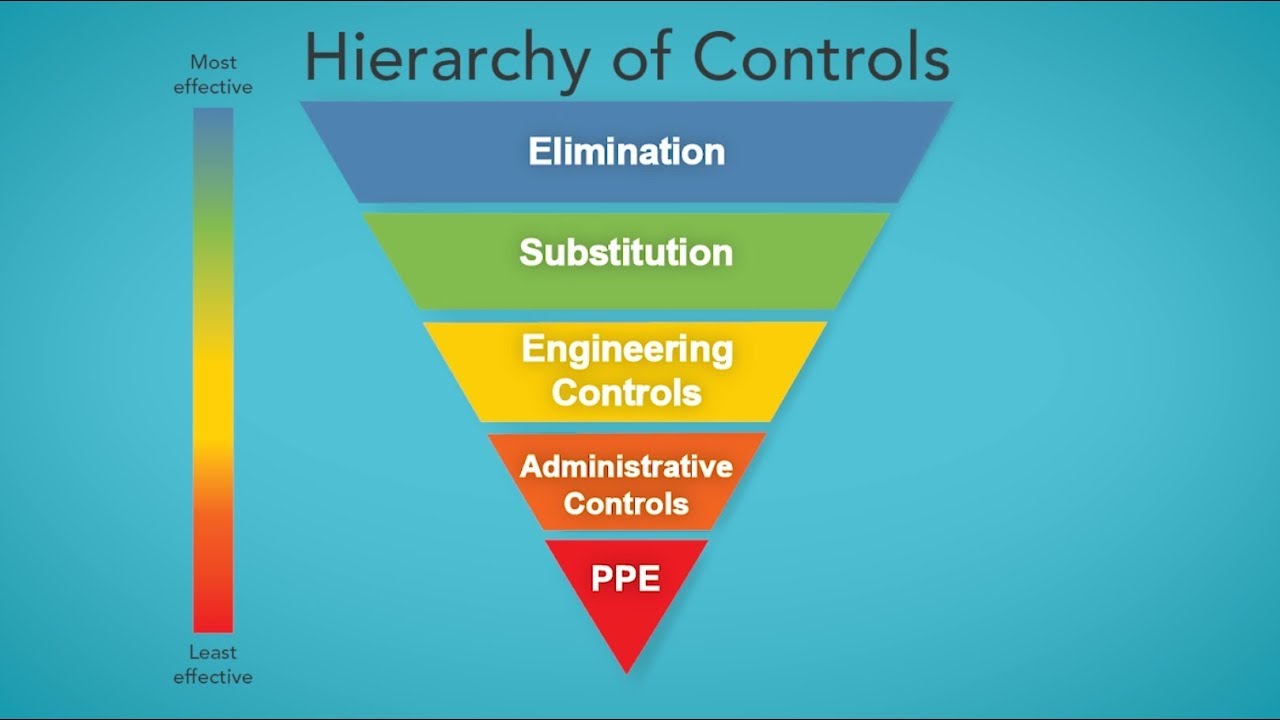
You need sufficient resources to make it possible.
Management success is all about planning, implementing and tracking change. In order to make the change a success, it must engage people and mobilize their commitment. The Human Side of Change Leadership identifies the possible reasons that a planned change will fail, and how to design motivation into the new process. There are 15 common waste scenarios that can result from a poor change management system. These scenarios illustrate what could go wrong and why.
FAQ
It seems so difficult sometimes to make sound business decisions.
Complex business systems have many moving parts. They require people to manage multiple priorities and deal with uncertainty and complexity.
The key to making good decisions is to understand how these factors affect the system as a whole.
You must first consider what each piece of the system does and why. It is important to then consider how the individual pieces relate to each other.
You need to ask yourself if your previous actions have led you to make unfounded assumptions. If you don't have any, it may be time to revisit them.
You can always ask someone for help if you still have questions after all of this. They may see things differently from you and have insights that could help you find a solution.
What is the difference between TQM and Six Sigma?
The main difference between these two quality management tools is that six sigma focuses on eliminating defects while total quality management (TQM) focuses on improving processes and reducing costs.
Six Sigma is a methodology for continuous improvement. This approach emphasizes eliminating defects through statistical methods like control charts, Pareto analysis, and p-charts.
This method seeks to decrease variation in product output. This is accomplished through identifying and correcting root causes.
Total quality management is the measurement and monitoring of all aspects within an organization. It also involves training employees to improve performance.
It is often used to increase productivity.
What are the five management processes?
These five stages are: planning, execution monitoring, review and evaluation.
Planning involves setting goals for the future. It involves setting goals and making plans.
Execution happens when you actually do the plan. They must be followed by all parties.
Monitoring is the act of monitoring your progress towards achieving your targets. Monitoring should include regular reviews of performance against goals and budgets.
Every year, there are reviews. They give you an opportunity to review the year and assess how it went. If not, changes may be made to improve the performance next time around.
After each year's review, evaluation occurs. It helps to determine what worked and what didn’t. It also provides feedback regarding how people performed.
What are the three main management styles you can use?
These are the three most common management styles: participative (authoritarian), laissez-faire (leavez-faire), and authoritarian. Each style has strengths and flaws. Which style do your prefer? Why?
Authoritarian - The leader sets the direction and expects everyone to comply with it. This style is most effective when an organization is large, stable, and well-run.
Laissez-faire: The leader lets each person decide for themselves. This style works best when the organization is small and dynamic.
Participative - Leaders listen to all ideas and suggestions. This is a great style for smaller organizations that value everyone.
How can we create a successful company culture?
A company culture that values and respects its employees is a successful one.
It is founded on three basic principles:
-
Everybody has something to offer.
-
People are treated fairly
-
There is mutual respect between individuals and groups
These values can be seen in the behavior of people. They will treat others with consideration and courtesy.
They will respect other people's opinions.
And they will encourage others to share ideas and feelings.
The company culture promotes collaboration and open communication.
People feel comfortable expressing their opinions freely without fear of reprisal.
They know that they will not be judged if they make mistakes, as long as the matter is dealt with honestly.
Finally, the company culture promotes integrity and honesty.
Everyone knows that they must always tell truth.
Everyone knows that there are rules and regulations that apply to them.
Nobody expects to be treated differently or given favors.
Statistics
- As of 2020, personal bankers or tellers make an average of $32,620 per year, according to the BLS. (wgu.edu)
- The average salary for financial advisors in 2021 is around $60,000 per year, with the top 10% of the profession making more than $111,000 per year. (wgu.edu)
- The BLS says that financial services jobs like banking are expected to grow 4% by 2030, about as fast as the national average. (wgu.edu)
- The profession is expected to grow 7% by 2028, a bit faster than the national average. (wgu.edu)
- Hire the top business lawyers and save up to 60% on legal fees (upcounsel.com)
External Links
How To
How can Lean Manufacturing be done?
Lean Manufacturing techniques are used to reduce waste while increasing efficiency by using structured methods. They were created by Toyota Motor Corporation in Japan in the 1980s. It was designed to produce high-quality products at lower prices while maintaining their quality. Lean manufacturing is about eliminating redundant steps and activities from the manufacturing process. It is composed of five fundamental elements: continuous improvement; pull systems, continuous improvements, just-in–time, kaizen, continuous change, and 5S. It is a system that produces only the product the customer requests without additional work. Continuous improvement involves constantly improving upon existing processes. Just-in-time refers to when components and materials are delivered directly to the point where they are needed. Kaizen is continuous improvement. This can be achieved by making small, incremental changes every day. Fifth, the 5S stand for sort, set up in order to shine, standardize, maintain, and standardize. These five elements are used together to ensure the best possible results.
Lean Production System
Six key concepts underlie the lean production system.
-
Flow is about moving material and information as near as customers can.
-
Value stream mapping - Break down each stage in a process into distinct tasks and create an overview of the whole process.
-
Five S's: Sort, Shine Standardize, Sustain, Set In Order, Shine and Shine
-
Kanban - use visual signals such as colored tape, stickers, or other visual cues to keep track of inventory;
-
Theory of constraints: Identify bottlenecks and use lean tools such as kanban boards to eliminate them.
-
Just-in time - Get components and materials delivered right at the point of usage;
-
Continuous improvement - Make incremental improvements rather than overhauling the entire process.