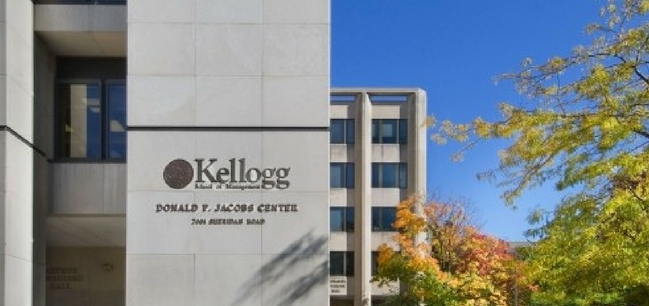
There are four stages that a person who is going through a transformation will experience. These are Denial and Resistance, Exploration, Engagement, and Commitment. Each stage presents its own challenges. To get through them, you must identify what you're trying to replace and what you're keeping. These will assist you in the transition process.
Denial
When we face change, we typically experience four stages, ranging from denial to commitment. The Stage of Shock can be described as a brief-term reaction. It is characterized as a decline in productivity as the brain processes news and reality. This stage is known as the Stage of Denial and can last for quite a while. If you're unable to move on from this stage, it can lead to an eventual loss of touch with reality.
This phase allows people to try to maintain their current state of affairs while trying to avoid change. Their energy can fluctuate with their performance and they might feel sad or angry. This phase is critical and it's important to have supportive structures. You must face the reality that change is imminent and be determined to forge a new path.
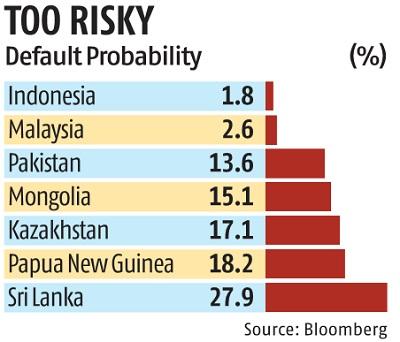
Resistance
To determine the impact of temperature on nickel alloy resistance near the ferromagnetic Phase Transition, a study was carried out. A large hydrostatic cubic multiple-anvil pressure chamber was used to measure the nickel resistance at 25 and 45 Kbar. The result was a computer-controlled, real-time measurement system. The measurements showed that there was a good agreement between the resistance measured at atmospheric and high pressures. In addition, they showed that the critical temperature, Tc, increases with pressure at a rate of 0.193+-0.013 K/kbar.
These measurements show that phase transition resistance results from the Tdependent gap function. This resistance stays constant at low temperatures. If the temperature goes above the critical threshold, the resistance increases in the intergranular zone. The sensitivity of this feature shows that the resistive features of the junction are SNS.
Exploration
The Exploration Phase is crucial for a transition. It allows you to strengthen organizational capacity and find out more about the program or practice. This phase involves engaging community stakeholders and professionals in the implementation process. The goal is to identify the needs of the program/practice and develop solutions that meet them. The Exploration Phase consists of identifying the most essential components of a program or practice, and defining what the scope of work is.
A team called the Implementation Team is responsible for creating, scaling up, and maintaining usable innovations. These teams are able to integrate drivers, stages, or improvement cycles into one integrated process. This process may begin with a single person bringing new ways of working into the organization. But it could also include the formation of a team that can be key to the sustainability process.
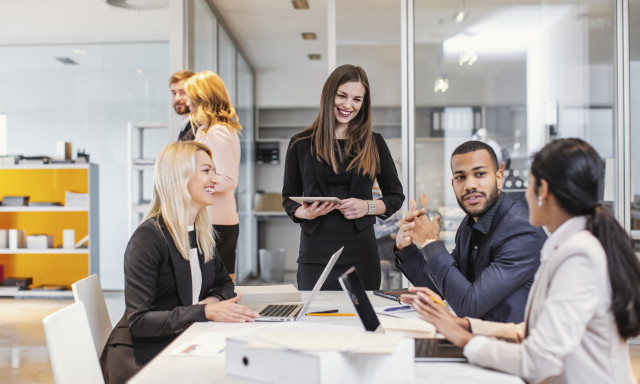
Commitment
Commitment to a change initiative is often accompanied by several phases. These phases are characterized as a lack of skills and setting, and an insufficient ability to make the necessary changes. When these phases pass, people will either continue in the same state or move to a new stage. Individuals who are determined to take on a change initiative will be more likely make progress.
The Contact Stage is where employees are exposed to the new initiative. The Contact Stage allows employees to be exposed to the new initiative. This might be through poor financial statements, meetings with the CEO, or meetings with senior staff.
FAQ
How can a manager improve his/her managerial skills?
It is important to have good management skills.
Managers must constantly monitor the performance of their subordinates.
You must quickly take action if your subordinate fails to perform.
You should be able pinpoint what needs to improve and how to fix it.
How do you effectively manage employees?
Achieving employee happiness and productivity is key to managing them effectively.
This also involves setting clear expectations and monitoring their performance.
Managers must set clear goals for their employees and themselves to achieve this goal.
They should communicate clearly to staff members. They need to communicate clearly with their staff.
They must also keep track of the activities of their team. These include:
-
What was accomplished?
-
How much work did you put in?
-
Who did it?
-
How did it get done?
-
Why it was done?
This information is useful for monitoring performance and evaluating the results.
What is TQM?
The quality movement was born during the industrial revolution when manufacturing companies realized they could not compete on price alone. They needed to improve quality and efficiency if they were going to remain competitive.
Management responded to the need to improve, and developed Total Quality Management (TQM). This focused on improving every aspect of an organization’s performance. It involved continuous improvement, employee participation, and customer satisfaction.
Statistics
- Your choice in Step 5 may very likely be the same or similar to the alternative you placed at the top of your list at the end of Step 4. (umassd.edu)
- As of 2020, personal bankers or tellers make an average of $32,620 per year, according to the BLS. (wgu.edu)
- The average salary for financial advisors in 2021 is around $60,000 per year, with the top 10% of the profession making more than $111,000 per year. (wgu.edu)
- The BLS says that financial services jobs like banking are expected to grow 4% by 2030, about as fast as the national average. (wgu.edu)
- Our program is 100% engineered for your success. (online.uc.edu)
External Links
How To
What is Lean Manufacturing?
Lean Manufacturing methods are used to reduce waste through structured processes. These processes were created by Toyota Motor Corporation, Japan in the 1980s. The goal was to produce quality products at lower cost. Lean manufacturing focuses on eliminating unnecessary steps and activities from the production process. It is composed of five fundamental elements: continuous improvement; pull systems, continuous improvements, just-in–time, kaizen, continuous change, and 5S. Pull systems are able to produce exactly what the customer requires without extra work. Continuous improvement is constantly improving upon existing processes. Just-in-time is when components and other materials are delivered at their destination in a timely manner. Kaizen stands for continuous improvement. Kaizen can be described as a process of making small improvements continuously. Five-S stands for sort. It is also the acronym for shine, standardize (standardize), and sustain. These five elements can be combined to achieve the best possible results.
Lean Production System
Six key concepts make up the lean manufacturing system.
-
Flow - focus on moving material and information as close to customers as possible;
-
Value stream mapping - break down each stage of a process into discrete tasks and create a flowchart of the entire process;
-
Five S’s - Sorted, In Order. Shine. Standardize. And Sustain.
-
Kanban – visual signals like colored tape, stickers or other visual cues are used to keep track inventory.
-
Theory of constraints: Identify bottlenecks and use lean tools such as kanban boards to eliminate them.
-
Just-in Time - Send components and material directly to the point-of-use;
-
Continuous improvement - Make incremental improvements rather than overhauling the entire process.