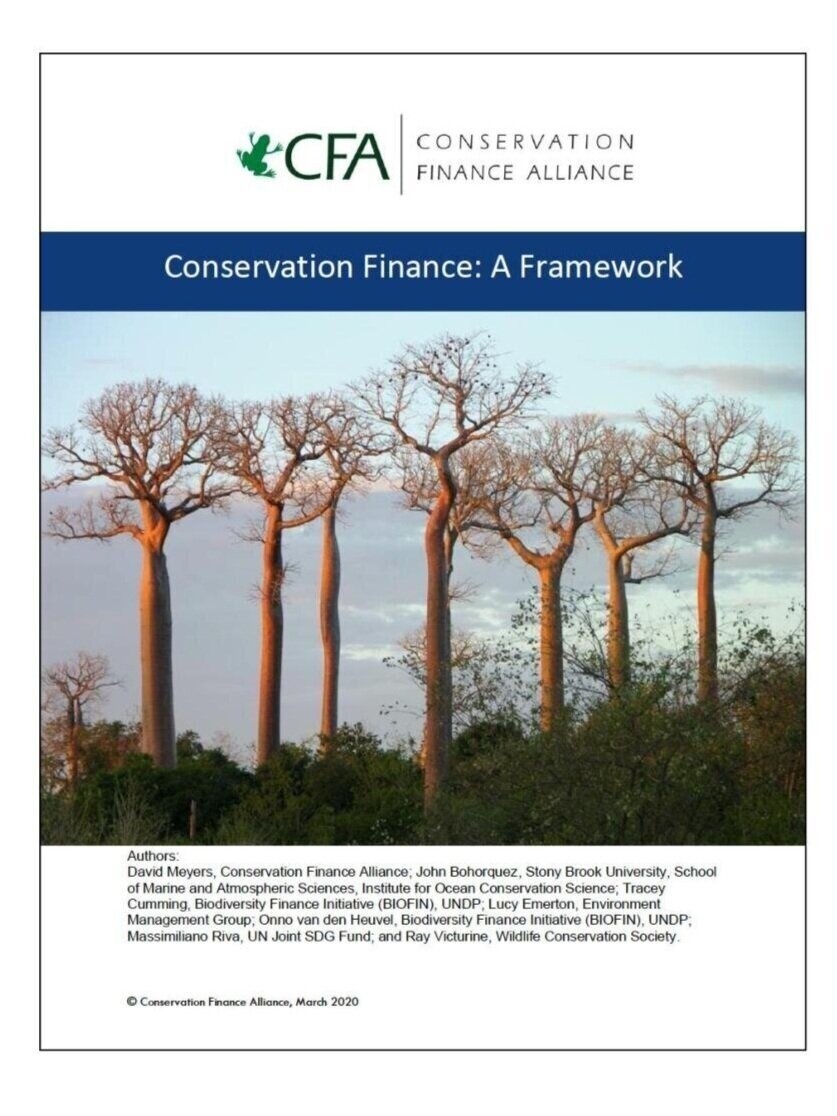
Tasks are an essential component of project management. Without them, a project cannot begin. It is impossible to begin writing an article without having decided on the topic, and created a draft. Before you publish it, it is important to have someone review it. A project cannot start without meeting a specific task, such a requirement. These tasks, also known as constraints, are essential to manage the project to avoid creating a bottleneck or setback.
Identifying task dependencies
A critical aspect of project management is the identification of task dependencies. This relationship between tasks determines the order in which a project needs to be completed. The ability to identify dependencies between tasks can help you create realistic timelines. It also helps you manage stakeholder expectation. For example, a device must be completed before QA test it. The same applies to software development projects. All development must be finished before the QA team can test it.
Gantt charts are a visual tool that project managers can use to track the dependencies among tasks. Gantt chart dependencies are indicated by an arrow connecting the tasks. You can identify tasks that have dependencies by using a whiteboard and digital whiteboard. A project manager can also use a project management app like Miro Powe-Up to keep track of the status of their tasks.
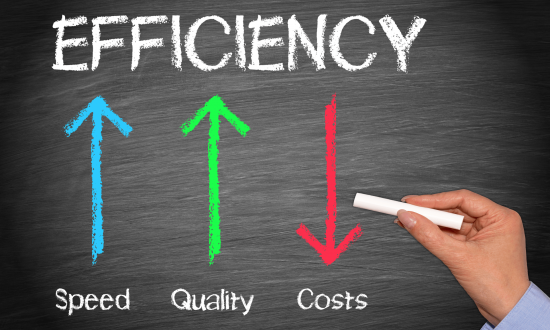
Management of recurring tasks
You can set up recurring tasks to be carried out periodically if you have a project schedule. These tasks can be assigned to occur on a set day of week, monthly, and/or annually. To ensure that they are not forgotten, you can set the start and end dates for recurring tasks.
You can streamline your project by using recurring tasks. They also help you manage your work load. These tasks can remind you about daily or weekly tasks and can even notify other devices. Manage recurring task will help you meet deadlines as well as manage the schedules for your team members.
Identifying resource needs
Project management is about identifying the resource requirements. Companies can use resource planning to avoid bottlenecks, and it helps them calculate the skills required. It can reduce overloads, improve employee satisfaction, and help to decrease overstaffing. It can enhance the performance and efficiency of project managers when resource planning is done correctly.
Resources are the foundation of a project's plan. At the portfolio or at the business level, resource management charts and resource lists can be created to show availability and use. Identifying resource costs and capabilities requires accurate planning and communication. For example, it is important to calculate the direct costs of each resource, as well as the billed rate to the client. Take into account lead times when ordering physical resource.
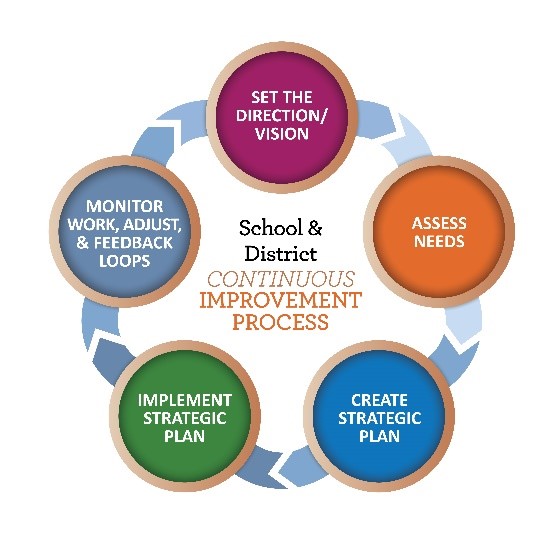
Communication with colleagues
Communication with team members is best when there is an open policy. This allows everyone to voice their concerns and questions, and it will build trust among your team members. Open doors allow for free communication between all team members and reduces physical barriers. It is important to offer constructive criticism when it is appropriate, but make sure it is clear, concise, and useful.
You should communicate regularly with your team, regardless of what type of project it is. It means setting up regular meetings, and updating your team members. Everybody should be invited to project meetings. They should also be informed of their responsibilities. To increase communication between team members, you can hold team-building activities such as role-plays and dinners. These exercises can help employees feel connected and feel like they are part of a second extended family.
FAQ
What is Six Sigma?
It's a strategy for quality improvement that emphasizes customer care and continuous learning. This is an approach to quality improvement that uses statistical techniques to eliminate defects.
Motorola's 1986 efforts to improve manufacturing process efficiency led to the creation of Six Sigma.
It was quickly adopted by the industry and many companies are now using six-sigma to improve product design, production, delivery, customer service, and product design.
What is the difference in leadership and management?
Leadership is all about influencing others. Management is about controlling others.
A leader inspires his followers while a manager directs the workers.
Leaders motivate people to succeed; managers keep workers on track.
A leader develops people; a manager manages people.
Six Sigma is so beloved.
Six Sigma is easy to use and can lead to significant improvements. Six Sigma provides a framework to measure improvements and allows companies to focus on the most important things.
What are some common mistakes managers make?
Managers can make their jobs more difficult than necessary.
They might not give enough support and delegate the right responsibilities to their staff.
Managers often lack the communication skills necessary to motivate and guide their teams.
Some managers create unrealistic expectations for their teams.
Managers might try to solve every problem by themselves rather than delegating the responsibility.
What is a basic management tool that can be used for decision-making?
A decision matrix, a simple yet powerful tool for managers to make decisions, is the best. They can think about all options and make informed decisions.
A decision matrix is a way to organize alternatives into rows and columns. It is easy to see how each option affects the other options.
This example shows four options, each represented by the boxes on either side of the matrix. Each box represents one option. The top row displays the current situation, and the bottom row shows what might happen if nothing is done.
The effect of selecting Option 1 is shown in the middle column. It would increase sales by $2 million to 3 million in this instance.
The results of choosing Option 2 and 3 can be seen in the columns below. These positive changes result in increased sales of $1 million and $500,000. These positive changes have their downsides. Option 2, for example, increases the cost by $100 000 while Option 3 decreases profits by $200 000.
Finally, the last column shows the results of choosing Option 4. This would result in a reduction of sales of $1 million.
The best part about using a decision matrix to guide you is that you don’t need to keep track of which numbers go where. You can just glance at the cells and see immediately if one given choice is better.
This is because the matrix has already taken care of the hard work for you. It is as simple as comparing the numbers within the relevant cells.
Here's a sample of how you might use decision matrixes in your business.
It is up to you to decide whether to spend more money on advertising. By doing so, you can increase your revenue by $5 000 per month. However, additional expenses of $10 000 per month will be incurred.
You can calculate the net result of investing in advertising by looking at the cell directly below the one that says "Advertising." That number is $15 thousand. Therefore, you should choose to invest in advertising since it is worth more than the cost involved.
How do you manage employees effectively?
Managing employees effectively means ensuring that they are happy and productive.
It is important to set clear expectations about their behavior and keep track of their performance.
Managers must be clear about their goals and those of their teams in order to succeed.
They need to communicate clearly and openly with staff members. They must communicate clearly with staff members.
They must also keep track of the activities of their team. These include:
-
What did we accomplish?
-
How much work did you put in?
-
Who did it, anyway?
-
Was it done?
-
Why it was done?
This information can be used to monitor performance and evaluate results.
Statistics
- The average salary for financial advisors in 2021 is around $60,000 per year, with the top 10% of the profession making more than $111,000 per year. (wgu.edu)
- As of 2020, personal bankers or tellers make an average of $32,620 per year, according to the BLS. (wgu.edu)
- 100% of the courses are offered online, and no campus visits are required — a big time-saver for you. (online.uc.edu)
- The BLS says that financial services jobs like banking are expected to grow 4% by 2030, about as fast as the national average. (wgu.edu)
- Your choice in Step 5 may very likely be the same or similar to the alternative you placed at the top of your list at the end of Step 4. (umassd.edu)
External Links
How To
How does Lean Manufacturing work?
Lean Manufacturing processes are used to reduce waste and improve efficiency through structured methods. They were developed by Toyota Motor Corporation in Japan during the 1980s. It was designed to produce high-quality products at lower prices while maintaining their quality. Lean manufacturing is about eliminating redundant steps and activities from the manufacturing process. It includes five main elements: pull systems (continuous improvement), continuous improvement (just-in-time), kaizen (5S), and continuous change (continuous changes). It is a system that produces only the product the customer requests without additional work. Continuous improvement is constantly improving upon existing processes. Just-in time refers to components and materials being delivered right at the place they are needed. Kaizen means continuous improvement. Kaizen involves making small changes and improving continuously. Finally, 5S stands for sort, set in order, shine, standardize, and sustain. These five elements work together to produce the best results.
Lean Production System
Six key concepts underlie the lean production system.
-
Flow is about moving material and information as near as customers can.
-
Value stream mapping- This allows you to break down each step of a process and create a flowchart detailing the entire process.
-
Five S's – Sort, Put In Order Shine, Standardize and Sustain
-
Kanban – visual signals like colored tape, stickers or other visual cues are used to keep track inventory.
-
Theory of constraints: identify bottlenecks in your process and eliminate them using lean tools, such as kanban board.
-
Just-in-time - deliver components and materials directly to the point of use;
-
Continuous improvement is making incremental improvements to your process, rather than trying to overhaul it all at once.