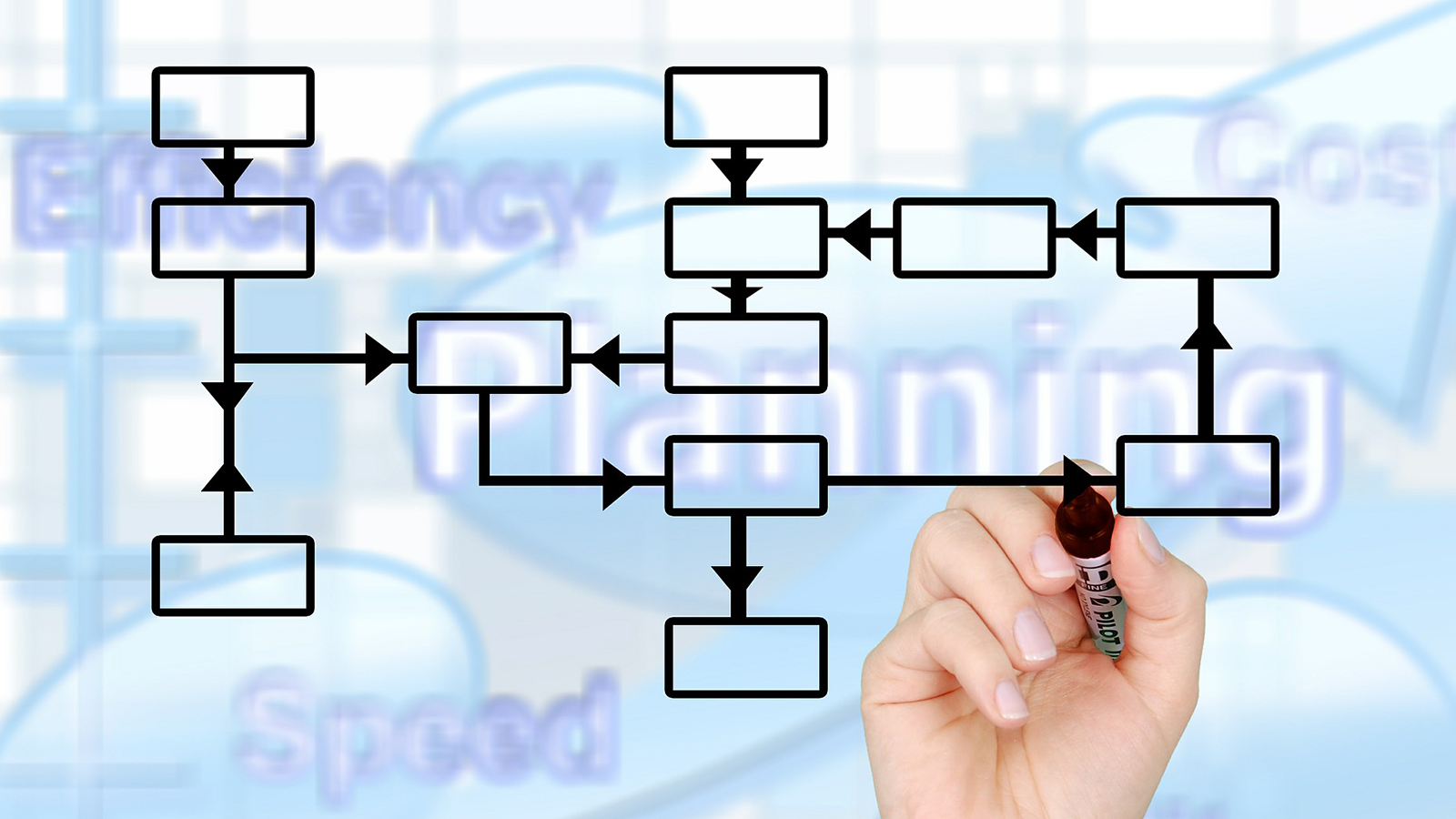
Extension of the supply chain is next in healthcare delivery. The supply chain must go beyond the hospital walls, and must incorporate last-mile transportation. Telemedicine, at-home testing kits and Telehealth all require healthcare supply chains that extend beyond the hospital. This article will examine some key indicators that a supply chain is healthy.
Indicators for supply chain performance
The importance of monitoring and managing the supply chains is vital for the success of healthcare facilities. Key Performance Indicators, or KPIs, are powerful tools that can be used for internal monitoring and improvement of decision-making. KPIs are available at all levels of an organisation, from doctors to nurses. This paper examines the relative importance and validation of KPIs related to healthcare.
Supply chains are only as successful as their ability to support patient care. Supply chain managers provide data that hospitals can use to improve patient care. They can help improve patient safety and ensure that treatment processes are efficient.
Reliability and stability of the supply chains
Reliability of the systems is one of the most critical aspects of healthcare logistics. This reliability can depend on the context and be crucial in meeting patient requirements and maintaining continuity of care. A reliable supply network is vital for the continuity of patient flow and services to hospitals and clinics.
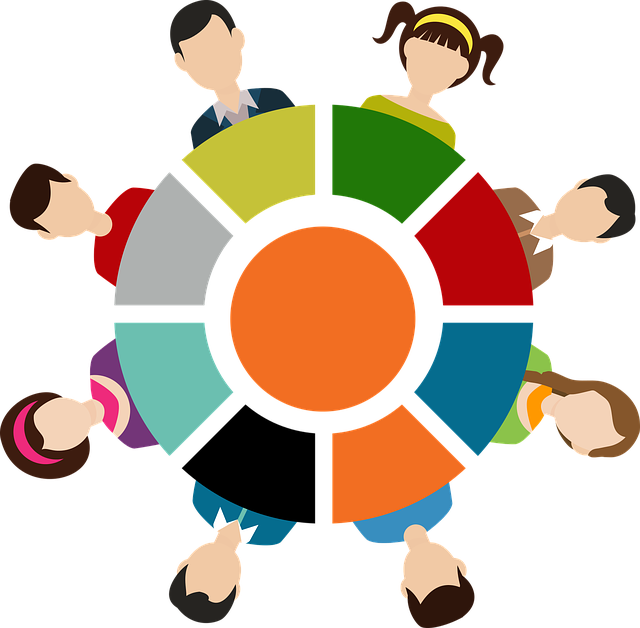
Reliability in healthcare can be measured by assessing three key elements: timeliness, effectiveness, and patient focus. These processes must deliver the required medication to patients at the appropriate time and to the right place. These three factors are essential, but a reliable healthcare supply chain must also be tied to a patient-centric approach to integrated action.
Interconnectivity
Interconnectivity is a key benefit for the industry of health care. It can provide patients with fast, same-day delivery and on-demand access to needed medical services. Fortunately, the supply chain can help make this vision a reality. Companies are developing innovative solutions to meet patient-centric needs, including flexible last-mile and direct-to-consumer deliveries.
In order to combat emerging diseases and promote health, it is essential that we improve the delivery of health care. Many healthcare systems are working to improve the efficiency and effectiveness of their operations and to reduce costs. They are also working to create and foster integrated operations, which involve all stakeholders. Recent years have seen a rapid increase in healthcare research. This has led to a self-sustaining discipline for operations.
Points of Entry
The supply chain of healthcare products is plagued by many problems. A misalignment among incentives is one of these problems. Healthcare industry is faced with increasing costs, increased regulations, and many other challenges. Healthcare organizations must have better visibility into the goods they purchase and ship to address these issues. This means that they must develop strategic partnerships to find ways to overcome these challenges.
A healthcare supply chain is a series of interrelated relationships that help provide superior customer value at lower costs. This chain begins at the manufacturer of the medicine or healthcare supply and moves through distribution centers and hospitals. Hospitals can buy medicine from the manufacturer directly or through a distributor. Distributors buy medicines in bulk and keep a large supply of medicines at their locations.
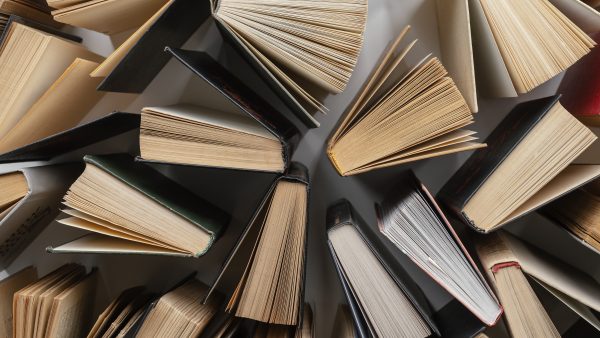
Human capital
Human capital is an essential part of the healthcare supply chains. It helps manage the resources, the quality of service, and the satisfaction of workers. This asset can be valuable if managed well. It will improve the productivity of businesses and increase the value of employees if it is managed well.
Human capital management is a collection of organizational practices aimed at building and maintaining employee engagement. Employee engagement is crucial to a company's success, and can be measured through a variety of measures. Gallup says that business units with high employee engagement have 40% fewer quality incidents, 10 percent more customer metrics and 20% higher sales.
FAQ
Six Sigma is so popular.
Six Sigma can be implemented quickly and produce impressive results. It provides a framework that allows for improvement and helps companies concentrate on what really matters.
What role can a manager fill in a company’s management?
There are many roles that a manager can play in different industries.
A manager generally manages the day to-day operations in a company.
He/she ensures that the company meets its financial obligations and produces goods or services that customers want.
He/she makes sure that employees adhere to the rules and regulations as well as quality standards.
He/she is responsible for the development of new products and services, as well as overseeing marketing campaigns.
How does a manager motivate their employees?
Motivation refers to the desire or need to succeed.
Doing something that is enjoyable can help you get motivated.
You can also feel motivated by making a positive contribution to the success in the organization.
For example, if you want to become a doctor, you'll probably find it more motivating to see patients than to study medicine books all day.
The inner motivation is another type.
Perhaps you have a strong sense to give back, for example.
You might even enjoy the work.
Ask yourself why you feel so motivated.
Next, think of ways you can improve your motivation.
What are some common management mistakes?
Sometimes managers make their job harder than they need to.
They may not be able to delegate enough responsibility to staff or provide adequate support.
A majority of managers lack the communication skills needed to motivate their team and lead them.
Managers set unrealistic expectations and make it difficult for their team.
Managers may attempt to solve all problems themselves, rather than delegating it to others.
What's the difference between leadership & management?
Leadership is about inspiring others. Management is all about controlling others.
A leader inspires his followers while a manager directs the workers.
A leader motivates people and keeps them on task.
A leader develops people; a manager manages people.
Statistics
- Our program is 100% engineered for your success. (online.uc.edu)
- As of 2020, personal bankers or tellers make an average of $32,620 per year, according to the BLS. (wgu.edu)
- Hire the top business lawyers and save up to 60% on legal fees (upcounsel.com)
- 100% of the courses are offered online, and no campus visits are required — a big time-saver for you. (online.uc.edu)
- This field is expected to grow about 7% by 2028, a bit faster than the national average for job growth. (wgu.edu)
External Links
How To
How can Lean Manufacturing be done?
Lean Manufacturing uses structured methods to reduce waste, increase efficiency and reduce waste. They were created in Japan by Toyota Motor Corporation during the 1980s. The aim was to produce better quality products at lower costs. Lean manufacturing seeks to eliminate unnecessary steps and activities in the production process. It is composed of five fundamental elements: continuous improvement; pull systems, continuous improvements, just-in–time, kaizen, continuous change, and 5S. Pull systems are able to produce exactly what the customer requires without extra work. Continuous improvement involves constantly improving upon existing processes. Just-in time refers to components and materials being delivered right at the place they are needed. Kaizen means continuous improvement. Kaizen involves making small changes and improving continuously. The 5S acronym stands for sort in order, shine standardize and maintain. These five elements work together to produce the best results.
Lean Production System
Six key concepts form the foundation of the lean production system:
-
Flow - focus on moving material and information as close to customers as possible;
-
Value stream mapping is the ability to divide a process into smaller tasks, and then create a flowchart that shows the entire process.
-
Five S's – Sort, Put In Order Shine, Standardize and Sustain
-
Kanban is a visual system that uses visual cues like stickers, colored tape or stickers to keep track and monitor inventory.
-
Theory of Constraints - Identify bottlenecks in the process, and eliminate them using lean tools such kanban boards.
-
Just-in time - Get components and materials delivered right at the point of usage;
-
Continuous improvement - make incremental improvements to the process rather than overhauling it all at once.