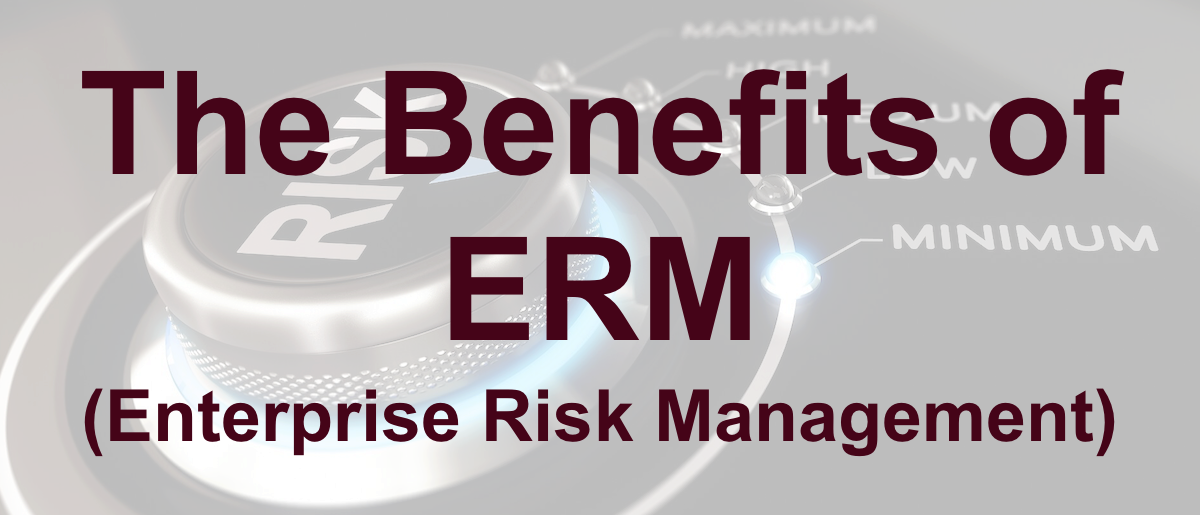
A certified construction manger is a professional who has been trained in the field. These professionals must pass a formal test to prove their proficiency. The practical exam tests the candidate's knowledge and skills in construction. The length of the exam depends on the qualifications. Passing the examination takes on average four hours.
Earnings potential
An attractive option is to get a degree as construction manager. The education required is typically four years, although it is possible to earn a master's in construction management in as little as one year. You will need to have one year of experience working under the supervision and guidance of a construction manager before you can start your journey towards certification.
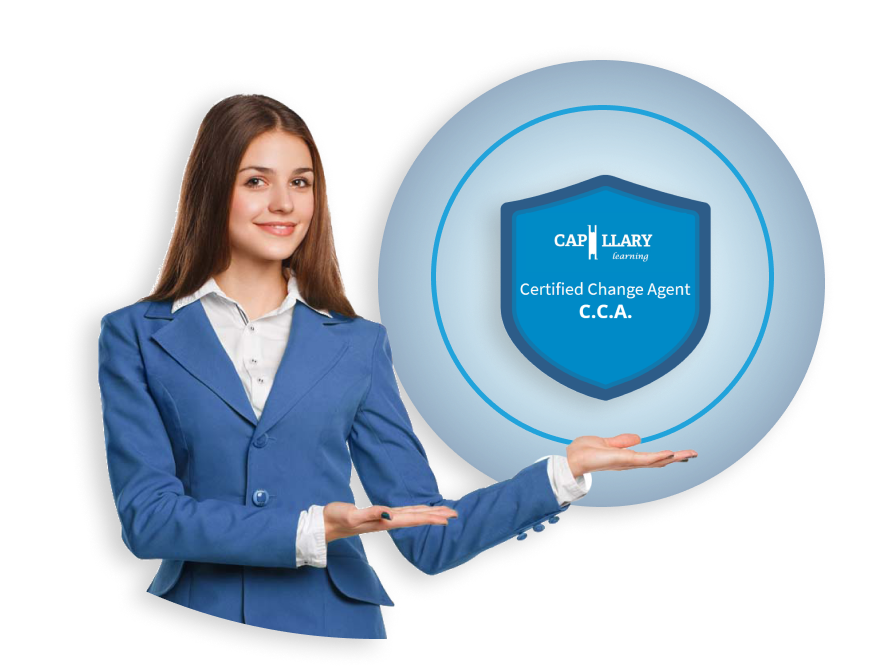
Earning a certificate for construction management can help increase your earnings potential and keep your licenses and certifications current. Certification courses can also help you stay current on safety and compliance guidelines.
Credentials required
Certification is a great way to increase your skills, whether you are looking to build a career as a construction manager or just to improve your resume. You will be able to prove your knowledge and commitment to the field. There are a variety of certifications available, and finding one that supports your career goals is crucial to your success.
You must pass a 600-question, six hour exam in order to earn the credential. The practical assessment tests your knowledge in safety and construction management. Once you pass the test, you can get access to a mentor directory and become a Certified Construction Manager. After you receive the credential, it can be used up to seven times, but you have to take it again after seven years.
Your job duties
A construction manager is an individual with special knowledge in building construction. To complete a project, they work closely with civil engineers as well as other building specialists. They negotiate and manage construction contracts. They supervise the selection of subcontractors as well as contractors. They may also interact directly with local government officials and lawyers.
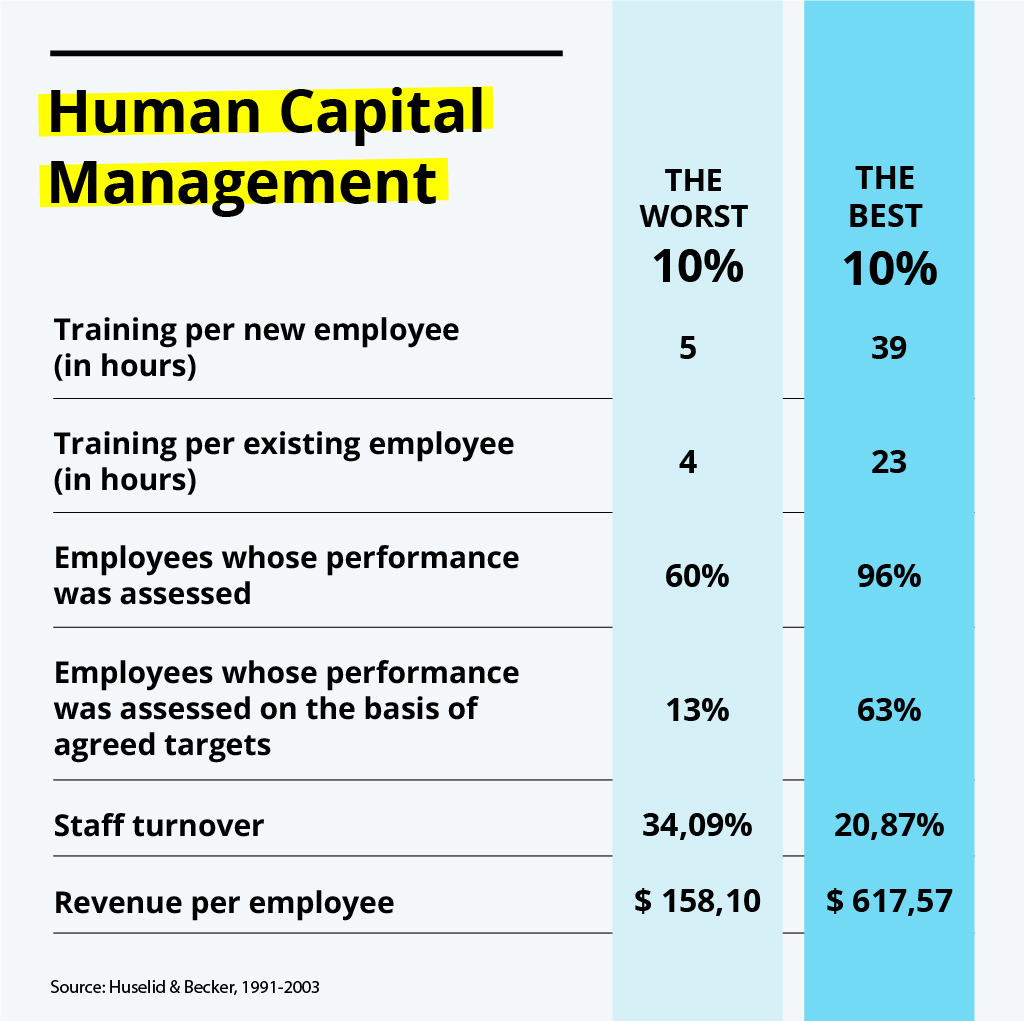
To ensure a successful construction project, construction managers must be capable of identifying and mitigating risks. They must also be able work with multiple teams to ensure the best possible construction. This job requires a bachelor's degree with at least five years experience in related work. A construction manager must also have exceptional communication skills to manage multiple audiences and address issues and disputes.
FAQ
What is a basic management tool used in decision-making?
A decision matrix can be a simple, but effective tool to assist managers in making decisions. It helps them to think strategically about all options.
A decision matrix represents alternatives in rows and columns. It is easy to see how each option affects the other options.
In this example, there are four possible options represented by boxes on the left-hand side of the matrix. Each box represents a different option. The top row displays the current situation, and the bottom row shows what might happen if nothing is done.
The effect of Option 1 can be seen in the middle column. In this case, it would mean increasing sales from $2 million to $3 million.
The results of choosing Option 2 and 3 can be seen in the columns below. These are positive changes - they increase sales by $1 million and $500 thousand respectively. However, these also involve negative consequences. Option 2 can increase costs by $100 million, while Option 3 can reduce profits by $200,000.
The final column shows results of choosing Option 4. This means that sales will decrease by $1 million.
The best part of using a decision-matrix is that it doesn't require you to know which numbers belong where. You can just glance at the cells and see immediately if one given choice is better.
The matrix has already done all of the work. It is as simple as comparing the numbers within the relevant cells.
Here's an example of how you might use a decision matrix in your business.
It is up to you to decide whether to spend more money on advertising. If you do this, you will be able to increase revenue by $5000 per month. But, you will also incur additional expenses of $10 thousand per month.
Look at the cell immediately below the one that states "Advertising" to calculate the net investment in advertising. It's $15,000. Advertising is worth more than its cost.
What is the difference in Six Sigma and TQM?
The main difference in these two quality management tools lies in the fact that six sigma is focused on eliminating defects and total quality management (TQM), emphasizes improving processes and reducing costs.
Six Sigma is a method for continuous improvement. This approach emphasizes eliminating defects through statistical methods like control charts, Pareto analysis, and p-charts.
This method has the goal to reduce variation of product output. This is achieved by identifying and addressing the root causes of problems.
Total quality management refers to the monitoring and measurement of all aspects in an organization. It also involves training employees to improve performance.
It is commonly used as a strategy for increasing productivity.
What are the four major functions of Management?
Management is responsible of planning, organizing, leading, and controlling people as well as resources. This includes setting goals, developing policies and procedures, and creating procedures.
Management aids an organization in reaching its goals by providing direction and coordination, control, leadership motivation, supervision, training, evaluation, and leadership.
Management has four primary functions:
Planning - This is the process of deciding what should be done.
Organizing – Organizing means deciding how to organize things.
Directing – This means to get people to follow directions.
Controlling - This is the ability to control people and ensure that they do their jobs according to plan.
What does Six Sigma mean?
Six Sigma uses statistical analyses to locate problems, measure them, analyze root cause, fix problems and learn from the experience.
The first step in solving a problem is to identify it.
The next step is to collect data and analyze it in order to identify trends or patterns.
Then corrective actions are taken to solve the problem.
The data are then reanalyzed to see if the problem is solved.
This cycle will continue until the problem is solved.
Statistics
- UpCounsel accepts only the top 5 percent of lawyers on its site. (upcounsel.com)
- The BLS says that financial services jobs like banking are expected to grow 4% by 2030, about as fast as the national average. (wgu.edu)
- This field is expected to grow about 7% by 2028, a bit faster than the national average for job growth. (wgu.edu)
- The average salary for financial advisors in 2021 is around $60,000 per year, with the top 10% of the profession making more than $111,000 per year. (wgu.edu)
- Hire the top business lawyers and save up to 60% on legal fees (upcounsel.com)
External Links
How To
How do you apply the Kaizen method to your life?
Kaizen means continuous improvement. The Japanese philosophy emphasizes small, incremental improvements to achieve continuous improvement. This term was created by Toyota Motor Corporation in 1950. It's a process where people work together to improve their processes continuously.
Kaizen, a Lean Manufacturing method, is one of its most powerful. In this concept, employees who are responsible for the production line must identify problems that exist during the manufacturing process and try to solve them before they become big issues. This will increase the quality and decrease the cost of the products.
Kaizen is a way to raise awareness about what's happening around you. So that there is no problem, you should immediately correct it if something goes wrong. If someone spots a problem while at work, they should immediately report it to their manager.
Kaizen is based on a few principles. We always start from the end product and move toward the beginning. For example, if we want to improve our factory, we first fix the machines that produce the final product. First, we fix machines that produce components. Next, we fix machines that produce raw material. Then, we fix those who work directly with the machines.
This approach is called 'kaizen' because it focuses on improving everything steps by step. Once we have finished fixing the factory, we return to the beginning and work until perfection.
To implement kaizen in your business, you need to find out how to measure its effectiveness. There are many ways you can determine if kaizen has been implemented well. One method is to inspect the finished products for defects. Another way is to check how much productivity has grown since kaizen was implemented.
Another way to know whether kaizen is working is to ask yourself why did you decide to implement kaizen. You were trying to save money or obey the law? Did you really believe it would lead to success?
If you answered yes to any one of these questions, congratulations! You're now ready to get started with kaizen.