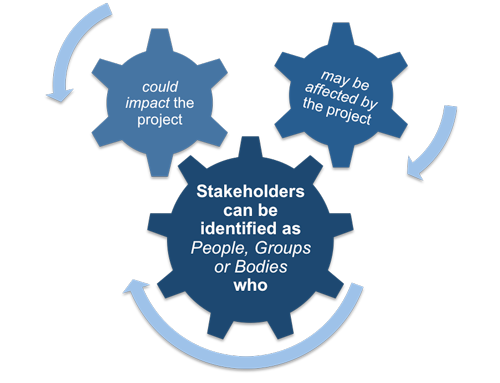
Waste management in Orlando: What are your responsibilities?
A waste management company is responsible for executing a wide range of services related to the management and treatment of waste. This includes municipal and private waste collection. These companies come up with innovative solutions for waste management that are compliant and environmentally friendly. Services offered include waste collection and recycling as well as disposal. They are also experts in bulk liquid and bulk solids management.
Waste management professionals also create policies and procedures for the proper handling of hazardous and contaminated wastes. These professionals ensure that hazardous and contaminated wastes are removed in compliance with local laws. Many waste professionals also work to make sure waste facilities operate efficiently and that their staff perform to the highest level.
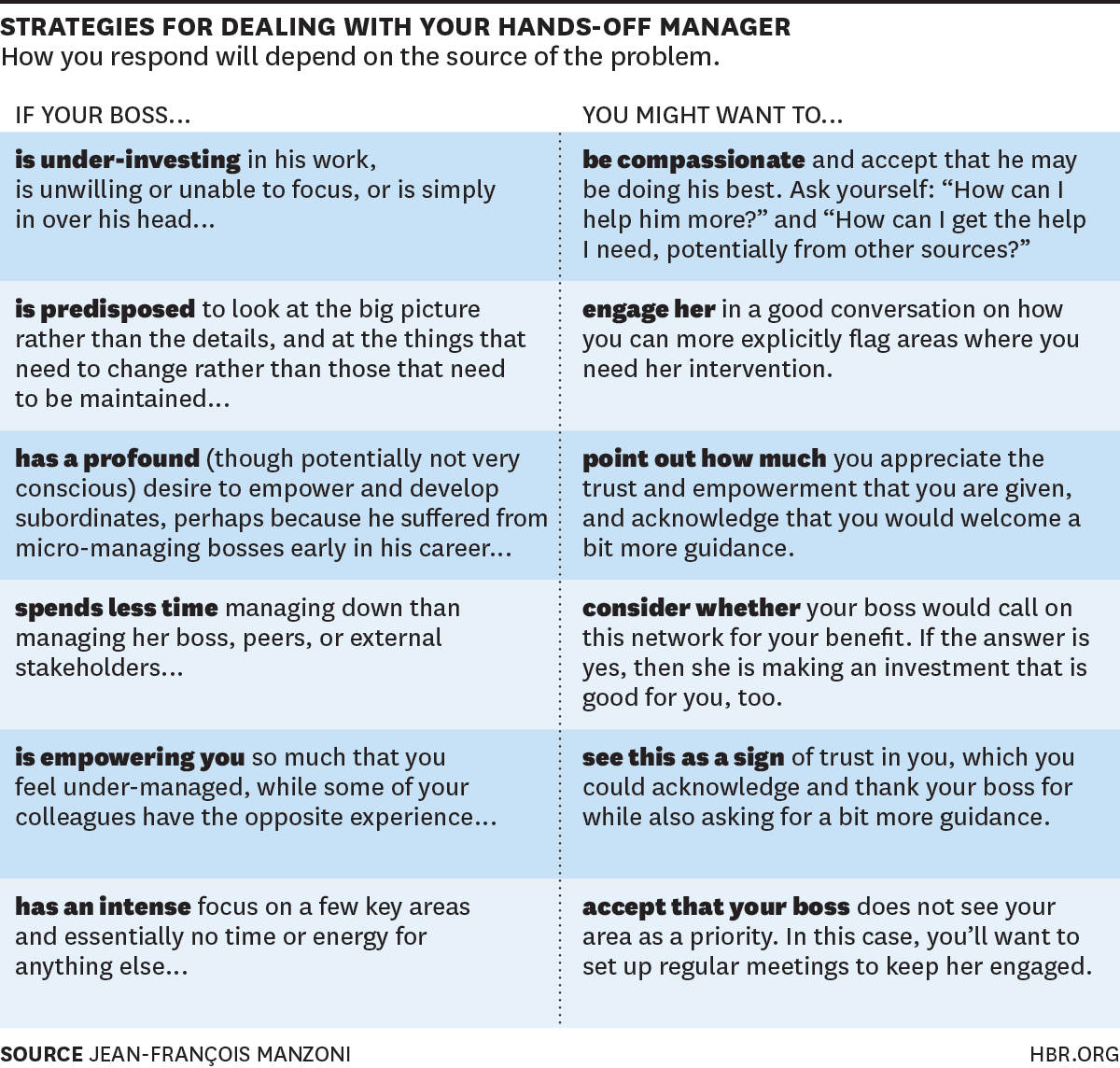
Salary for waste management companies in orlando
You might be curious about how much you can make in Orlando if you are interested in a career as a waste manager. The salaries for this job in Orlando, FL are quite good. The median salary for a waste manager is approximately $46,000. This is about 5% lower than the national mean and more that 25% less than salaries in other metros.
The average salary for this job in Orlando is $28,905. It is possible to expect a high income because of the competitive nature of Orlando's job market. You will receive a competitive total salary package that includes vacations, holidays, personal days, and paid vacation.
Companies that provide waste management services for orlando
Companies that offer waste management services in Orlando are able to help. Medical waste management is an integral part of any facility's waste management plan. UMI, for instance, offers medical waste management within Orlando and the Kissimmee vicinity. They offer a wide range of sharps containers, as well other waste containment options for healthcare facilities. They offer inventory management for sharps container collection containers.
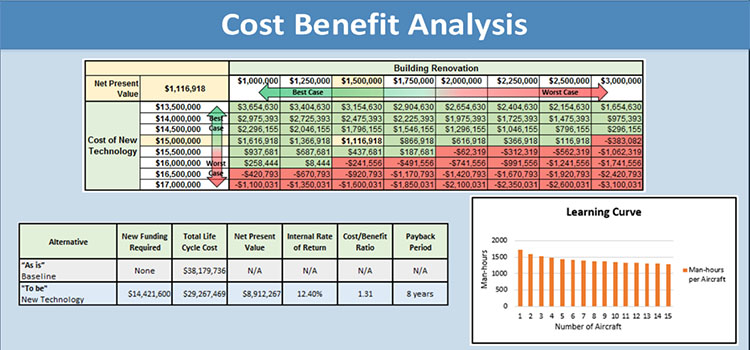
The Sunshine Recycling company provides waste management services in central Florida. It has partnered with Wawa Inc., a Pennsylvania-based convenience store and gas station combination franchise. Originally, Wawa operated stores in the New England area and then expanded south along the east coast, including Florida. The Wawa chain is well-known for its fast food and freshly prepared foods.
FAQ
What are the top management skills?
Business owners need to have management skills, no matter how small or large they may be. These include the ability and willingness to manage people, finances as well resources, time and space.
You will need management skills to set goals and objectives, plan strategies, motivate employees, resolve problems, create policies and procedures, and manage change.
As you can see there is no end to the number of managerial tasks.
What kind of people use Six Sigma
Six Sigma will most likely be familiar to people who have worked in statistics and operations research. It can be used by anyone in any business aspect.
It requires high levels of commitment and leadership skills to be successful.
What is a fundamental management tool for decision-making?
A decision matrix, a simple yet powerful tool for managers to make decisions, is the best. It helps them think systematically about all the options available to them.
A decision matrix is a way of representing alternatives as rows and columns. It is easy to see how each option affects the other options.
The boxes on the left hand side of this matrix represent four possible choices. Each box represents one option. The top row depicts the current status quo, while the bottom row represents what would happen if no action was taken.
The middle column shows the effect of choosing Option 1. It would increase sales by $2 million to 3 million in this instance.
The following columns illustrate the impact of Options 2 and 3. These positive changes can increase sales by $1 million or $500,000. These changes can also have negative effects. Option 2 can increase costs by $100 million, while Option 3 can reduce profits by $200,000.
The last column shows you the results of Option 4. This will result in sales falling by $1,000,000
A decision matrix has the advantage that you don’t have to remember where numbers belong. It's easy to see the cells and instantly know if any one of them is better than another.
This is because the matrix has already taken care of the hard work for you. It's simply a matter of comparing the numbers in the relevant cells.
Here is an example how you might use the decision matrix in your company.
You need to decide whether to invest in advertising. If you do, you'll be able to increase your revenue by $5 thousand per month. However, additional expenses of $10 000 per month will be incurred.
Look at the cell immediately below the one that states "Advertising" to calculate the net investment in advertising. It's $15,000. Advertising is worth much more than the investment cost.
What is the main difference between Six Sigma Six Sigma TQM and Six Sigma Six Sigma?
The major difference between the two tools for quality management is that six Sigma focuses on eliminating defect while total quality control (TQM), on improving processes and decreasing costs.
Six Sigma stands for continuous improvement. This method emphasizes eliminating defects using statistical methods such p-charts, control charts, and Pareto analysis.
This method aims to reduce variation in product production. This is accomplished through identifying and correcting root causes.
Total quality management refers to the monitoring and measurement of all aspects in an organization. It also includes training employees to improve performance.
It is frequently used as an approach to increasing productivity.
Statistics
- As of 2020, personal bankers or tellers make an average of $32,620 per year, according to the BLS. (wgu.edu)
- This field is expected to grow about 7% by 2028, a bit faster than the national average for job growth. (wgu.edu)
- 100% of the courses are offered online, and no campus visits are required — a big time-saver for you. (online.uc.edu)
- The profession is expected to grow 7% by 2028, a bit faster than the national average. (wgu.edu)
- Hire the top business lawyers and save up to 60% on legal fees (upcounsel.com)
External Links
How To
How can you implement the Kaizen technique?
Kaizen means continuous improvement. Kaizen is a Japanese concept that encourages constant improvement by small incremental changes. This is a collaborative process in which people work together to improve their processes continually.
Kaizen, a Lean Manufacturing method, is one of its most powerful. This concept requires employees to identify and solve problems during manufacturing before they become major issues. This way, the quality of products increases, and the cost decreases.
Kaizen is about making everyone aware of the world around them. So that there is no problem, you should immediately correct it if something goes wrong. If someone is aware of a problem at work, he/she should inform his/her manager immediately.
There are some basic principles that we follow when doing kaizen. Start with the end product, and then move to the beginning. If we want to improve our factory for example, we start by fixing the machines that make the final product. Next, we repair the machines that make components. Then, the machines that make raw materials. Then, we fix those who work directly with the machines.
This is known as "kaizen", because it emphasizes improving each step. We finish fixing the factory and then go back to the beginning. This continues until we achieve perfection.
You need to know how to measure the effectiveness of kaizen within your business. There are many ways you can determine if kaizen has been implemented well. Another method is to see how many defects are found on the products. Another way to find out how productive your company has been since you implemented kaizen is to measure the increase in productivity.
To determine if kaizen is effective, you should ask yourself why you chose to implement kaizen. Did you do it because it was legal or to save money? Did you really believe that it would be a success factor?
Let's say you answered yes or all of these questions. Congratulations! You're ready to start kaizen.