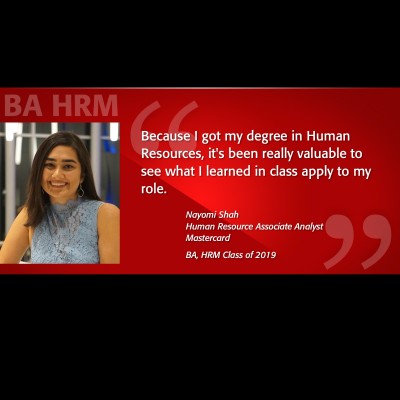
Casella is a leader in the manufacture of environmental monitoring equipment and occupational hygiene supplies. It is a regional, vertically integrated solid-waste services company that is based in Rutland. It was founded with just one truck in 1975. Despite increasing landfill fees and collection prices, the company has become a dominant player in the industry's waste disposal. Read on to learn about the company's history and future plans.
Casella is a leader in the manufacturing of environmental monitoring equipment and occupational hygiene products.
Casella is a global manufacturer and distributor of industrial monitoring equipment and environmental health monitoring equipment. They are committed to helping businesses reduce safety and health risks. Since 1799, Casella has been manufacturing precision instruments. They have also supplied Charles Darwin and David Livingstone. The company today provides reliable equipment and data management solutions to ensure that organizations comply with safety and health regulations.
The company's products range from personal sampling pumps and noise monitors to air quality monitors and pollution detection systems. They are versatile and can detect environmental threats, including air pollution. Casella sells equipment for personal hygiene and environmental monitoring. Save 10% on Casella equipment
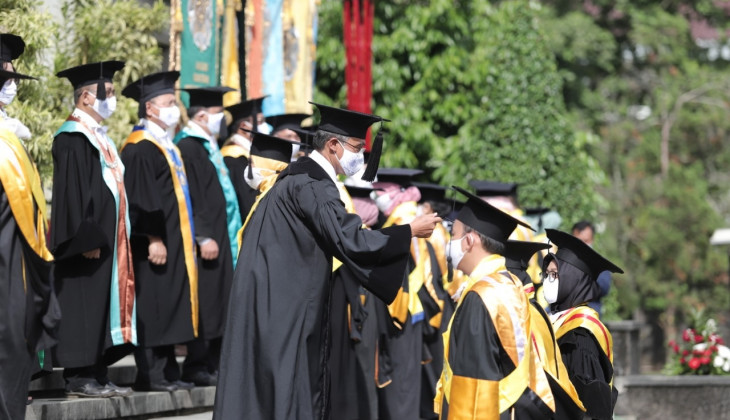
It employs a hierarchical management structure
A hierarchy is necessary for complex societies. Without hierarchy, arbitrary rule can be created and tyranny may emerge. We must be able to distinguish between the good and bad aspects of hierarchy, and promote those that are better. While hierarchy in business is complex, some work has been done. Below are some examples and implications of good and bad hierarchies. We'll be discussing how these types of hierarchy can help your business.
It boasts a large vehicle fleet
Casella's large fleet of vehicles is used to serve its many business needs. Casella is home to more than 50 of these vehicles. In addition, the company employs in-house mechanics to maintain its trucks and buses. Casella's impressive credit history has allowed them to manage 50 trucks and buses. Casella currently has approximately 5,000 employees across the country.
The Casella team uses technology to monitor driver activities and track productions to increase fuel efficiency and decrease idle time. Fleet management software is used by the company to monitor vehicle fuel consumption and idle time. This reduces fuel consumption while saving money. Casella dispatcher sees the drivers' current location and can spot any inefficient driving habits and help with vehicle maintenance in real time. Fleet management software allows managers to compare drivers according to productions, hours and commodities.
It raises landfill tip costs and raises collection rates
Casella is raising its prices as the trash industry struggles to find enough landfill space. Although many companies raise their prices because of lack of competition, Casella is increasing its prices largely due to increased competition. Since 2005, Casella has raised landfill tip fees. It has also increased collection prices by more that 4%. In its February earnings conference, the company stated that it would raise its landfill disposal prices by another 4%. However, the company's price hikes are not a sign that it is getting out of bed.
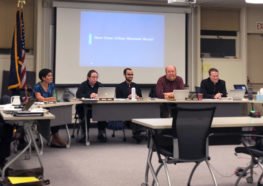
The company is known for its good corporate citizenship in Vermont. The company was once criticized for its poor contract practices. Today, the company is a large corporation with revenues of four billion dollars. It operates landfills, recycling centres, transfer stations, and collection roads. Casella has steadily grown to take control of Vermont's trash industry. Many business and consumer owners worry that Casella's rising costs could lead to them losing business.
FAQ
Which kind of people use Six Sigma
Six Sigma is well-known to those who have worked in operations research and statistics. Anyone involved in business can benefit.
Because it requires a high level of commitment, only those with strong leadership skills will make an effort necessary to implement it successfully.
What are the 4 main functions of management?
Management is responsible for organizing, managing, directing and controlling people, resources, and other activities. This includes setting goals, developing policies and procedures, and creating procedures.
Management helps an organization achieve its objectives by providing direction, coordination, control, leadership, motivation, supervision, training, and evaluation.
These are the four major functions of management:
Planning - Planning is about determining what must be done.
Organizing - Organization involves deciding what should be done.
Directing – This means to get people to follow directions.
Controlling - Controlling means ensuring that people carry out tasks according to plan.
How does Six Sigma work
Six Sigma uses statistical analyses to locate problems, measure them, analyze root cause, fix problems and learn from the experience.
The first step to solving the problem is to identify it.
Next, data are collected and analyzed in order to identify patterns and trends.
Then corrective actions are taken to solve the problem.
Final analysis of data is done to determine if the problem has been solved.
This cycle will continue until the problem is solved.
What is TQM?
The industrial revolution led to the birth and growth of the quality movement. Manufacturing companies realized they couldn't compete solely on price. To remain competitive, they had to improve quality as well as efficiency.
Management developed Total Quality Management to address the need for improvement. It focused on all aspects of an organisation's performance. It involved continuous improvement, employee participation, and customer satisfaction.
What are management theories?
Management Concepts are the management principles and practices that managers use in managing people and resources. They cover topics like job descriptions (job descriptions), performance evaluations, training programmes, employee motivation and compensation systems.
How can we create a successful company culture?
A culture of respect and value within a company is key to a productive culture.
It is founded on three basic principles:
-
Everybody has something of value to share
-
Fair treatment of people is the goal
-
Respect is shared between individuals and groups
These values reflect in how people behave. They will treat others with respect and kindness.
They will respect the opinions of others.
These people will inspire others to share thoughts and feelings.
Company culture also encourages open communication, collaboration, and cooperation.
People feel comfortable expressing their opinions freely without fear of reprisal.
They understand that errors will be tolerated as long they are corrected honestly.
Finally, the company culture promotes integrity and honesty.
Everyone knows that they must always tell truth.
Everyone knows that there are rules and regulations that apply to them.
People don't expect special treatment or favors.
What is the difference of leadership and management?
Leadership is about influence. Management is all about controlling others.
A leader inspires others while a manager directs them.
A leader inspires others to succeed, while a manager helps workers stay on task.
A leader develops people; a manager manages people.
Statistics
- The profession is expected to grow 7% by 2028, a bit faster than the national average. (wgu.edu)
- Hire the top business lawyers and save up to 60% on legal fees (upcounsel.com)
- The average salary for financial advisors in 2021 is around $60,000 per year, with the top 10% of the profession making more than $111,000 per year. (wgu.edu)
- As of 2020, personal bankers or tellers make an average of $32,620 per year, according to the BLS. (wgu.edu)
- 100% of the courses are offered online, and no campus visits are required — a big time-saver for you. (online.uc.edu)
External Links
How To
How do I do the Kaizen Method?
Kaizen means continuous improvement. This term was first used by Toyota Motor Corporation in the 1950s. It refers to the Japanese philosophy that emphasizes continuous improvement through small incremental changes. It's a process where people work together to improve their processes continuously.
Kaizen is one the most important methods of Lean Manufacturing. In this concept, employees who are responsible for the production line must identify problems that exist during the manufacturing process and try to solve them before they become big issues. This is how you can improve the quality and lower the cost.
Kaizen is the idea that every worker should be aware of what is going on around them. Correct any errors immediately to avoid future problems. If someone is aware of a problem at work, he/she should inform his/her manager immediately.
Kaizen is based on a few principles. We always start from the end product and move toward the beginning. For example, if we want to improve our factory, we first fix the machines that produce the final product. First, we fix machines that produce components. Next, we fix machines that produce raw material. Then we fix the workers, who directly work with these machines.
This approach is called 'kaizen' because it focuses on improving everything steps by step. We finish fixing the factory and then go back to the beginning. This continues until we achieve perfection.
To implement kaizen in your business, you need to find out how to measure its effectiveness. There are many ways you can determine if kaizen has been implemented well. One of these ways is to check the number of defects found on the finished products. Another way is determining how much productivity increased after implementing kaizen.
A good way to determine whether kaizen has been implemented is to ask why. Is it because the law required it or because you want to save money. Did you really believe it would lead to success?
Let's say you answered yes or all of these questions. Congratulations! You're ready to start kaizen.