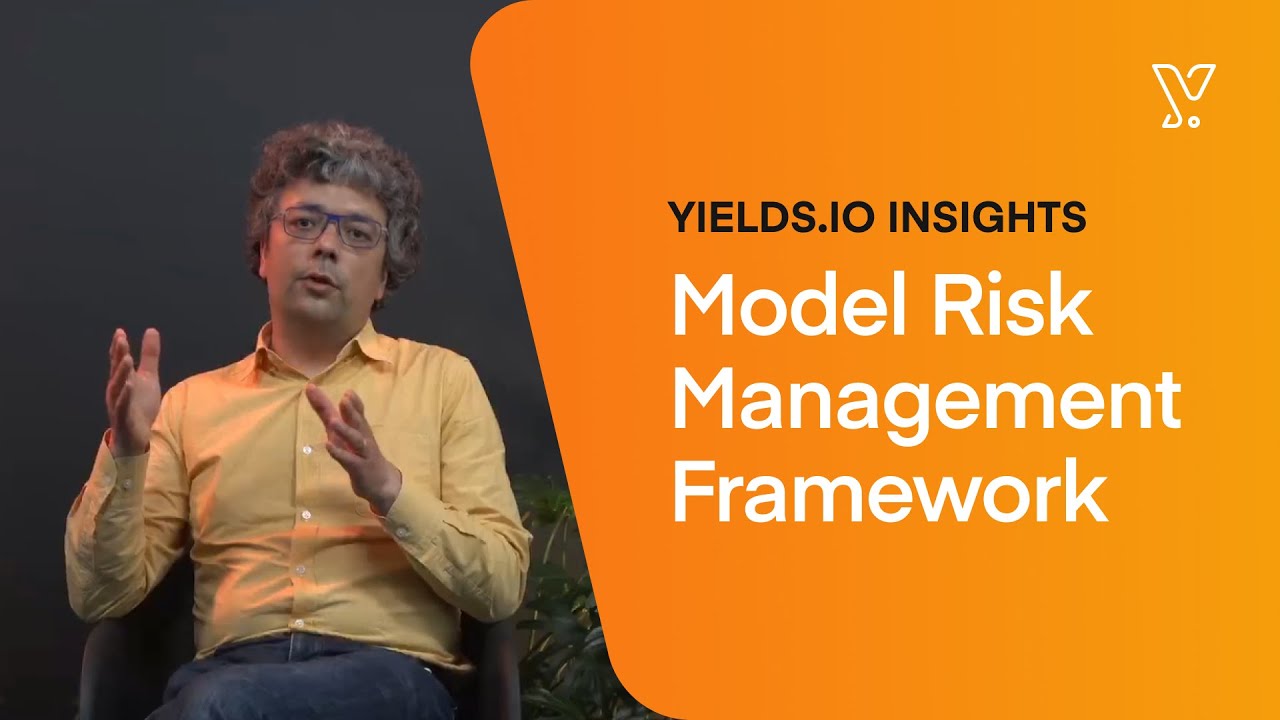
With more people involved in projects, project management is becoming a rapidly growing field. It is important to learn how to organize, manage, and deliver projects successfully. This guide will show newcomers how you can use the latest tools to manage your project. It includes information regarding milestones and Gantt charts as well as budgeting.
Scope verification
Scope validation is an essential step in project administration. The first step in project management is to ensure that the project remains within the original plan. You can do this through a variety of methods, including informal and formal walk-throughs. By defining a formal and informal validation process, a project manager can be sure that they have properly documented requirements, budgets, and deliverables for the project. Stakeholder interviews and surveys are another method for scope verification. The project manager should intervene if there are unrealistic expectations from stakeholder.
Scope verification is often carried out during the project lifecycle. It is often integrated into the project's last milestones, such customer signatures on deliverables. Deferring scope verification until the end of the project may result in rejection or rework.
Milestones
The use of milestones in project management can benefit all parties involved in the project. They can be used to avoid monotony and employee burnout, and they make it easier for stakeholders to see the status of the project. They can also be used to help organizations analyze past projects and make improvements to current projects. The ability to use milestones in cross-project overviews can make them easier to understand.
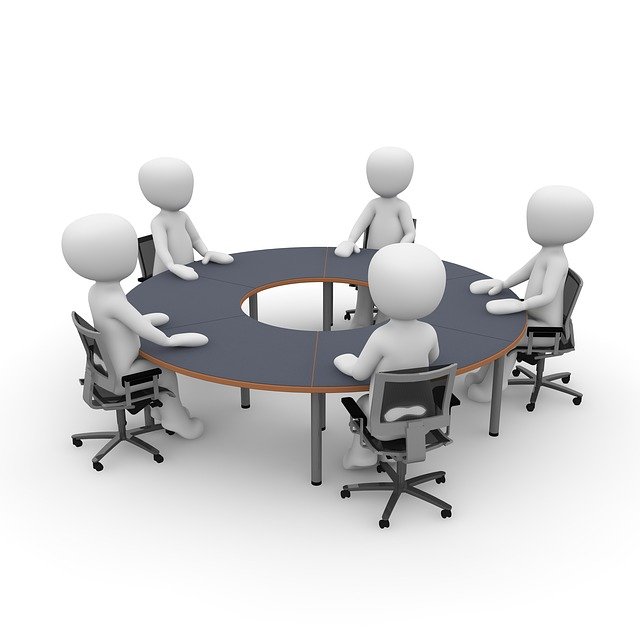
A milestone is not only helpful in project evaluation, but it also gives the entire team a sense if they have achieved something. Without milestones, the project may go on forever and lead to unrealistic plans or execution. Furthermore, project servers can become cluttered with content, so it's crucial that milestone plans stay on the project board as long as the project continues.
Gantt charts
Gantt diagrams are an effective tool in project management. Managers can use them to plan work and visually show the progress of each task. They were invented by Karol Adamiecki over a century ago. The idea of creating a bar chart that would show progress on a task caught the attention of other project managers, and it became an integral part of the construction industry. Gantt chart are an integral part most project management software today. They are used in a variety projects.
A Gantt chart is made up of columns that list task names and information. These columns can be followed by a bar chart. Task bars run horizontally, and begin at the start date. The longer the bar, the longer the task is expected to take.
Budgeting
One of the most important aspects of project management is budgeting. Budgeting for a project should be realistic. To decide which resources to use, the team should discuss all aspects. The team must also identify the potential risks involved in the project. Budgeting should include a contingency fund equal to 5-10% of the total project cost.
The team should first determine the scope and deliverables of the project before creating a budget. A work breakdown structure is also needed to document the work and resources required for the project.
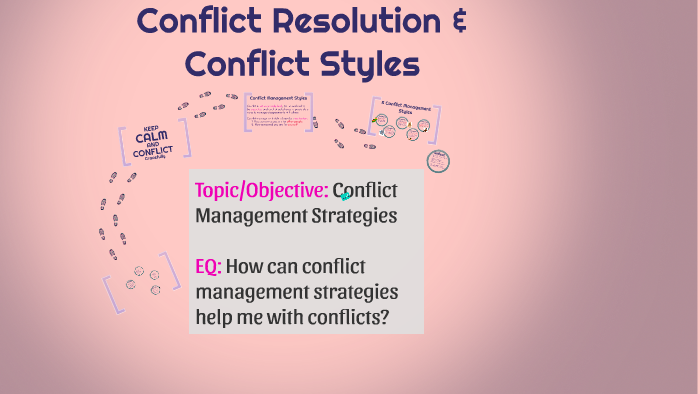
Team effort
Project management requires team effort. You can't manage projects well without team effort. Particularly, teamwork is the process of bringing together people from different backgrounds to bring out their best and create something new. Whether you work as an individual, part of a team, or on a project board, teamwork is essential.
Establishing the roles of each person is the first step in a team effort. Let them know how important they are to the project, as well as what their individual responsibilities are. In addition, explain what the project is about, and how the team will benefit if it is successful.
FAQ
What is a management tool to help with decision-making?
A decision matrix is an easy but powerful tool to aid managers in making informed decisions. They can think about all options and make informed decisions.
A decision matrix represents alternatives in rows and columns. This allows you to easily see how each choice affects others.
In this example, there are four possible options represented by boxes on the left-hand side of the matrix. Each box represents a different option. The top row shows the status quo (the current situation), and the bottom row shows what would happen if nothing was done at all.
The effect of Option 1 can be seen in the middle column. In this case, it would mean increasing sales from $2 million to $3 million.
The effects of options 2 and 3 are shown in the next columns. These are good changes, they increase sales by $1million or $500,000. They also have negative consequences. Option 2 increases costs by $100 thousand, while Option 3 decreases profits to $200 thousand.
The last column displays the results of selecting Option 4. This will result in sales falling by $1,000,000
The best part of using a decision-matrix is that it doesn't require you to know which numbers belong where. You can just glance at the cells and see immediately if one given choice is better.
The matrix already does all the work. It is as simple as comparing the numbers within the relevant cells.
Here's an example showing how you might use a Decision Matrix in your business.
It is up to you to decide whether to spend more money on advertising. If you do this, you will be able to increase revenue by $5000 per month. However, this will mean that you'll have additional expenses of $10,000.
You can calculate the net result of investing in advertising by looking at the cell directly below the one that says "Advertising." That number is $15 thousand. Advertising is worth more than its cost.
What is TQM, exactly?
The industrial revolution led to the birth and growth of the quality movement. Manufacturing companies realized they couldn't compete solely on price. They needed to improve quality and efficiency if they were going to remain competitive.
Management realized the need to improve and created Total Quality Management, which focused on improving all aspects within an organization's performance. It included continual improvement processes, employee involvement, customer satisfaction, and customer satisfaction.
How to manage employees effectively?
Managing employees effectively means ensuring that they are happy and productive.
It means setting clear expectations for them and keeping an eye on their performance.
Managers must set clear goals for their employees and themselves to achieve this goal.
They need to communicate clearly with staff members. They should also ensure that they both reward high performers and discipline those who are not performing to their standards.
They should also keep records of all activities within their team. These include:
-
What did we accomplish?
-
How much work were you able to accomplish?
-
Who did it?
-
Was it done?
-
Why was it done?
This information can be used to monitor performance and evaluate results.
What kind of people use Six Sigma
Six-sigma will be well-known to anyone who has worked in operations research or statistics. Anybody involved in any aspect or business can benefit.
It requires high levels of commitment and leadership skills to be successful.
Statistics
- UpCounsel accepts only the top 5 percent of lawyers on its site. (upcounsel.com)
- This field is expected to grow about 7% by 2028, a bit faster than the national average for job growth. (wgu.edu)
- Hire the top business lawyers and save up to 60% on legal fees (upcounsel.com)
- 100% of the courses are offered online, and no campus visits are required — a big time-saver for you. (online.uc.edu)
- The profession is expected to grow 7% by 2028, a bit faster than the national average. (wgu.edu)
External Links
How To
What is Lean Manufacturing?
Lean Manufacturing uses structured methods to reduce waste, increase efficiency and reduce waste. They were developed by Toyota Motor Corporation in Japan during the 1980s. The main goal was to produce products at lower costs while maintaining quality. Lean manufacturing seeks to eliminate unnecessary steps and activities in the production process. It has five components: continuous improvement and pull systems; just-in time; continuous change; and kaizen (continuous innovation). Pull systems allow customers to get exactly what they want without having to do extra work. Continuous improvement is the continuous improvement of existing processes. Just-in-time refers to when components and materials are delivered directly to the point where they are needed. Kaizen stands for continuous improvement. Kaizen can be described as a process of making small improvements continuously. Fifth, the 5S stand for sort, set up in order to shine, standardize, maintain, and standardize. These five elements are combined to give you the best possible results.
Lean Production System
The lean production system is based on six key concepts:
-
Flow - focus on moving material and information as close to customers as possible;
-
Value stream mapping: This is a way to break down each stage into separate tasks and create a flowchart for the entire process.
-
Five S’s - Sorted, In Order. Shine. Standardize. And Sustain.
-
Kanban is a visual system that uses visual cues like stickers, colored tape or stickers to keep track and monitor inventory.
-
Theory of constraints - identify bottlenecks during the process and eliminate them with lean tools like Kanban boards.
-
Just-in-time delivery - Deliver components and materials right to your point of use.
-
Continuous improvement - Make incremental improvements rather than overhauling the entire process.