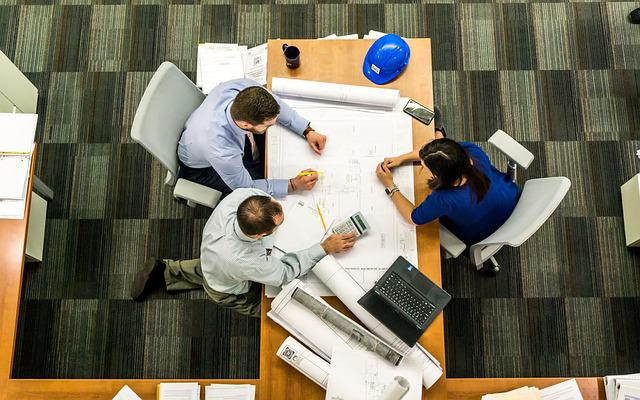
The Casella garbage company is a regional player in waste management in the Northeast. The company was recently accused of violating labor laws across three states. The stock rose 540% to $54 million after the company announced that it was consolidating its operations. According to the CEO, hardwork pays off.
Casella violated all three state labor laws
Three ex-drivers of Casella Waste Systems in Rutland sued the company over alleged violations to labor laws. They claim that they were not paid for routine overtime hours, and that their 30-minute meal breaks were automatically taken from their paychecks. Casella mandated that all drivers perform vehicle inspections prior to and after each trip. The plaintiffs are seeking damages as well as attorneys' fees.
Casella is an important regional player in Northeast's waste system
Casella, one of the leading regional players in waste management, has operations in New England, New York, and Pennsylvania. The company owns landfills, transfer stations, and recycling facilities. Its Rutland facility is the only open landfill in Vermont. It is listed on the stock exchange and anticipates revenue of $774 million by 2020. After markets close, the company reports its latest earnings.
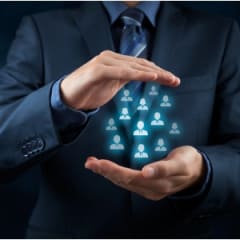
Casella shares have risen by 540% since the consolidated operations.
The stock of the company is trading at an all-time high, and has a market cap exceeding $1.8 billion. The company has risen from several bad decisions over the years to become one of New England's top garbage mover. Doug and John Casella founders are amongst the most well-off in the state. Additionally, they participate in the day to day operations of their company.
Casella's CEO explains that hard work pays off
Casella is a waste management, recycling and resource management company. World Finance Magazine has recently named Casella the most sustainable business in its sector. The company has achieved numerous record-setting accomplishments thanks to its commitment to sustainability and hard work.
Casella's stock closed at 55 cents per share
It was the lowest point in company history, closing at 55 cents per share on March 12, 2009. This was less than the twenty-seven times that it had in 1997. Casella is known for taking on substantial debts and has struggled financially in recent times. However, Casella made some business changes that could improve its prospects.
Casella's debt to finance a landfill development initiative
Casella has used debt to finance its landfill construction initiative. It hopes to get the new capacity online by the middle of 2023. The company is predicting further profitability over the next few years, and executives say they are confident that their business model can support future growth.
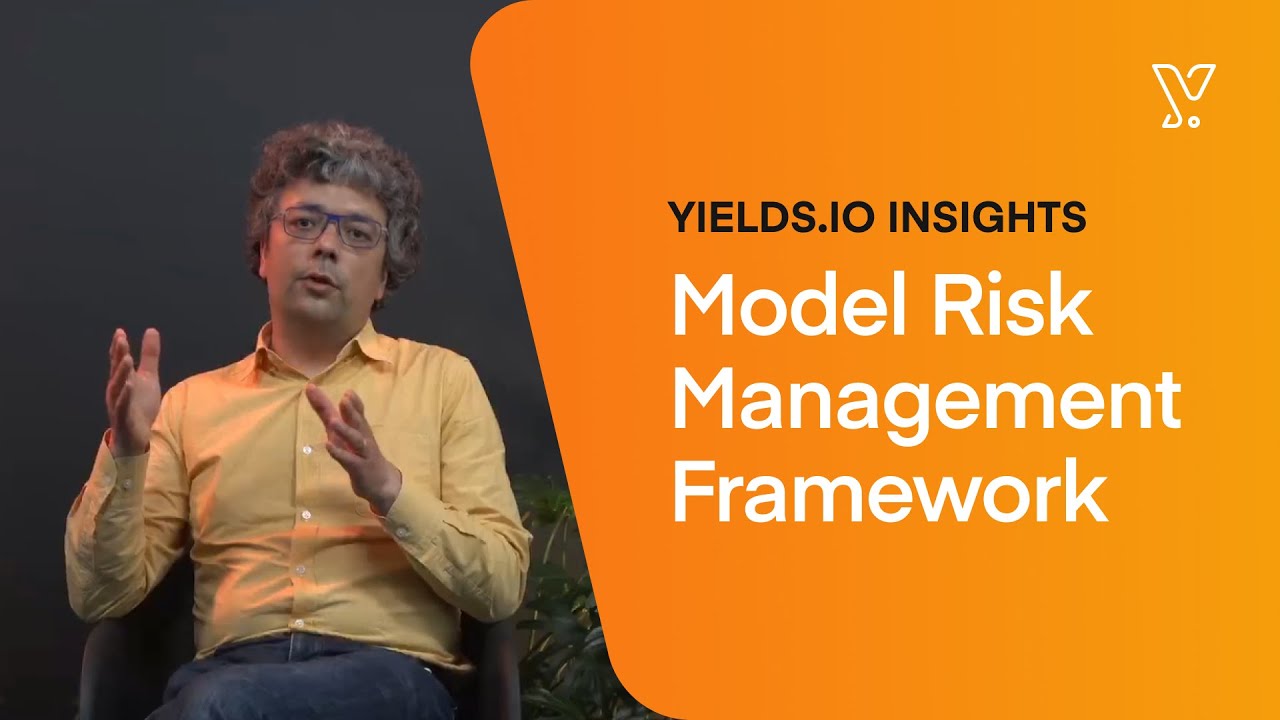
Casella's acquisition spree
Casella's acquisition spree has been nothing but a monumental undertaking. The company has already made at least six acquisitions, and invested in one company. In total, it has spent $355million. Casella's investments include waste management, construction, demolition, and raw materials.
FAQ
What are management theories?
Management Concepts are the principles and practices managers use to manage people and resources. These topics include job descriptions, performance evaluations and training programs. They also cover human resource policies, job description, job descriptions, job descriptions, employee motivation, compensation systems, organizational structures, and many other topics.
What can a manager do to improve his/her management skillset?
Through demonstrating good management skills at every opportunity
Managers must monitor the performance of subordinates constantly.
You must quickly take action if your subordinate fails to perform.
It is essential to know what areas need to be improved and how to do it.
What are some common management mistakes?
Sometimes managers make it harder for their employees than is necessary.
They may not delegate enough responsibilities to staff and fail to give them adequate support.
In addition, many managers lack the communication skills required to motivate and lead their teams.
Managers can set unrealistic expectations for their employees.
Managers might try to solve every problem by themselves rather than delegating the responsibility.
Which kind of people use Six Sigma
Six sigma is a common concept for people who have worked in statistics or operations research. It can be used by anyone in any business aspect.
It is a commitment-intensive task that requires strong leadership skills.
What is the difference of leadership and management?
Leadership is about influencing others. Management is all about controlling others.
A leader inspires followers while a manager directs workers.
Leaders motivate people to succeed; managers keep workers on track.
A leader develops people; a manager manages people.
Statistics
- Our program is 100% engineered for your success. (online.uc.edu)
- The profession is expected to grow 7% by 2028, a bit faster than the national average. (wgu.edu)
- 100% of the courses are offered online, and no campus visits are required — a big time-saver for you. (online.uc.edu)
- The BLS says that financial services jobs like banking are expected to grow 4% by 2030, about as fast as the national average. (wgu.edu)
- As of 2020, personal bankers or tellers make an average of $32,620 per year, according to the BLS. (wgu.edu)
External Links
How To
How can you implement the Kaizen technique?
Kaizen means continuous improvement. This term was first used by Toyota Motor Corporation in the 1950s. It refers to the Japanese philosophy that emphasizes continuous improvement through small incremental changes. It's a team effort to continuously improve processes.
Kaizen is one method that Lean Manufacturing uses to its greatest advantage. Kaizen is a concept where employees in charge of the production line are required to spot problems during the manufacturing process before they become major issues. This increases the quality of products and reduces the cost.
Kaizen is an approach to making every worker aware and alert to what is happening around them. Correct any errors immediately to avoid future problems. If someone spots a problem while at work, they should immediately report it to their manager.
When doing kaizen, there are some principles we must follow. When working with kaizen, we always start with the end result and move towards the beginning. In order to improve our factory's production, we must first fix the machines producing the final product. Next, we fix the machines which produce components. And finally, we fix the workers who work directly with those machines.
This is why it's called "kaizen" because it works step-by-step to improve everything. Once the factory is fixed, we return to the original site and work our way back until we get there.
It is important to understand how to measure the effectiveness and implementation of kaizen in your company. There are several ways to determine whether kaizen is working well. One method is to inspect the finished products for defects. Another way is determining how much productivity increased after implementing kaizen.
To determine if kaizen is effective, you should ask yourself why you chose to implement kaizen. Did you do it because it was legal or to save money? Did you really believe that it would be a success factor?
Let's say you answered yes or all of these questions. Congratulations! You are now ready to begin kaizen.