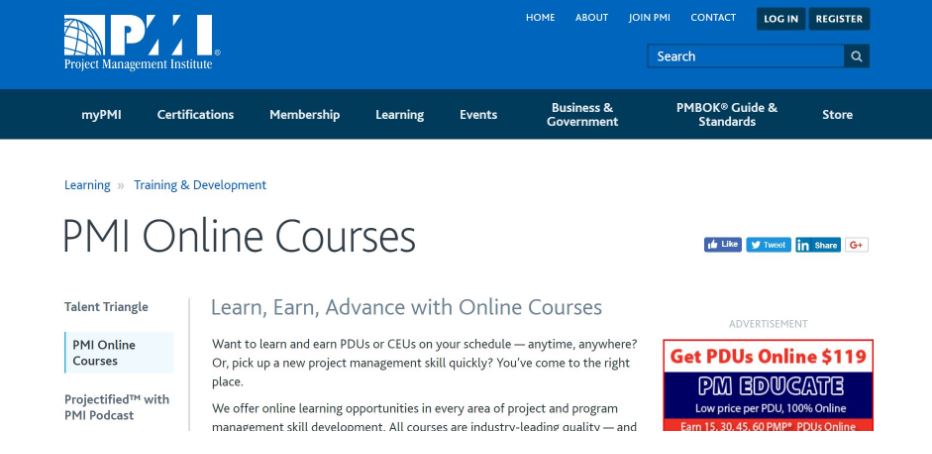
Supply chain financing is a great option to finance SMEs' operations. The benefits of this financing method include early payment of invoices, reduced credit risk, and extended payment terms. It's also an efficient way of getting short-term financing. This finance method is especially helpful for SMEs who might have difficulty obtaining bank loan.
Questions regarding supply chain financing
Supply chain financing has been called a risky business model in recent times. It can be beneficial for healthy companies but it can conceal a poor credit history and lead to further debts. This is especially true in supply chain finance, which may not be compliant with GAAP disclosure rules. Some media call this "hidden Debt"
Supply chain finance can be described as financing activity or operating cash-flow adjustments. Supply chain financing can be described as reverse factoring. This involves a seller sending an invoice on behalf of a buyer. This allows the seller and buyer to negotiate payment discounts and time frames. However, supply chain finance services can become complicated and confusing, and are susceptible to legal and regulatory issues.
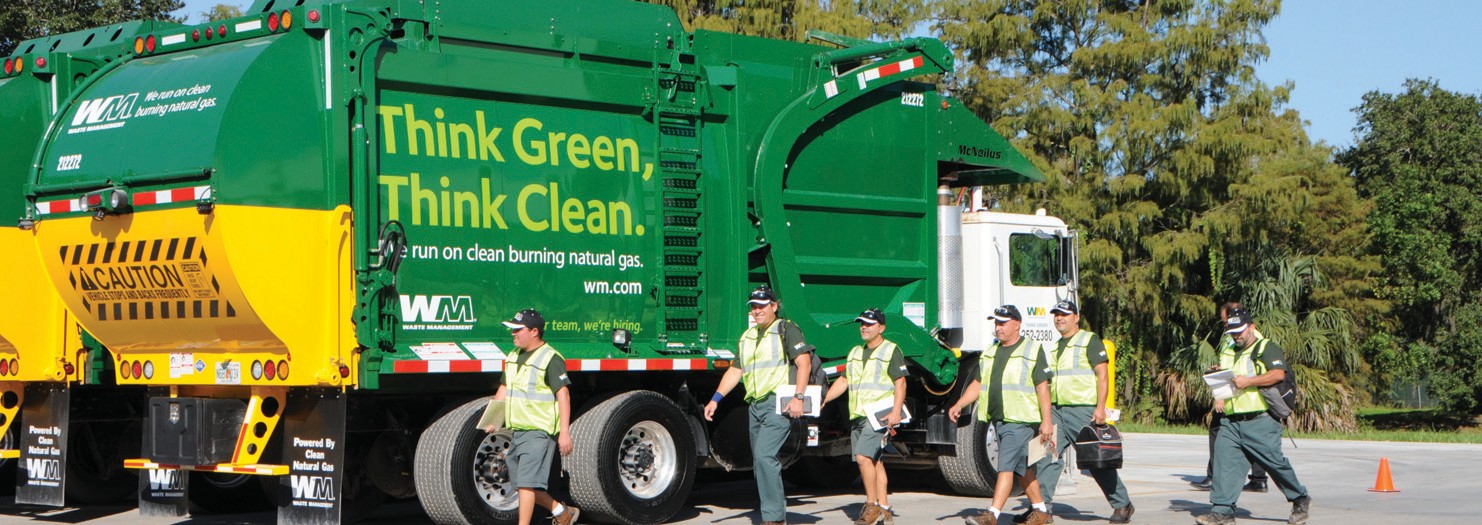
Suppliers are now more able and willing to accept early payment programs. But, suppliers must validate the reputation of the program they are participating in and evaluate its strength. Additionally, they must ensure that no third-party facilitates transactions or enforces accounting treatment.
Applying for supply chain financing
Suppliers and buyers have the option to extend payment terms through supply chain finance. The supplier sends the invoices to buyers, who then approve them and specify a maturity date. The lender advances up to 100% of the invoice to the supplier. The lender usually requires that the seller has a credit record of at least 2 years.
The supply chain financing funder can be either a traditional bank, or an alternative lending company like Fintech. The documentation must show evidence of goods/services rendered and the amount owed. It should also list the parties involved. These documents should also detail the payment terms. These documents will help increase the trust of the funding provider in extending the loan.
It is not always easy to obtain supply chain financing. Not only do they need to meet capital requirements but they also require that suppliers fulfill certain operational and financial criteria. Many of these programs require a Partner Financial Institution (PFI), a bank, or other non-bank entity to participate. A number of requirements must be met for the Partner Financial Institution to meet national safeguards and ADB integrity guidelines. They also need to comply with prudential regulations and clearances from government agencies.
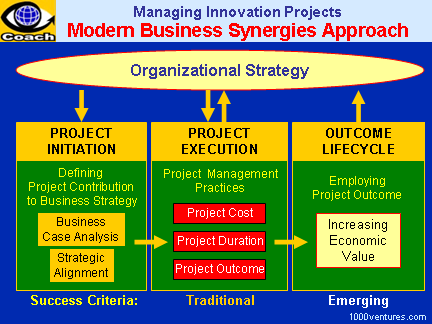
Supply chain financing terms and conditions
Supply chain financing helps companies meet their financial obligations. This involves the adjustment of a company's cash flow and the arrangement of financing to meet its business requirements. It is generally more affordable than traditional financing and benefits larger corporations. This financing is different than dynamic discounting which relies on a company's funds to finance a supplier.
This financing allows companies to increase their working capital and pay suppliers more quickly. It can also reduce days of unpaid sales. This helps companies plan and forecast cash flow better. Before attempting to finance supply chain, it is important that all parties are fully aware of the terms. It's best to use supply-chain finance only when it makes business sense.
Supply-chain finance programs typically record payments as accounts payable and not debt. This makes a company’s liquidity position appear stronger than is actually the case. Programs increase a company’s ability to borrow less but they do boost its working capital. They can also hide from investors some of the risk associated with supply-chain financing.
FAQ
What is TQM and how can it help you?
The industrial revolution led to the birth and growth of the quality movement. Manufacturing companies realized they couldn't compete solely on price. If they wanted to stay competitive, they needed to improve their quality and efficiency.
Management responded to the need to improve, and developed Total Quality Management (TQM). This focused on improving every aspect of an organization’s performance. It included continuous improvement processes, employee involvement, and customer satisfaction.
Why is Six Sigma so popular?
Six Sigma is easy and can deliver significant results. Six Sigma provides a framework to measure improvements and allows companies to focus on the most important things.
What role can a manager fill in a company’s management?
Each industry has a different role for a manager.
A manager is generally responsible for overseeing the day to day operations of a company.
He/she will ensure that the company fulfills its financial obligations.
He/she makes sure that employees adhere to the rules and regulations as well as quality standards.
He/she plans and oversees marketing campaigns.
What is a simple management tool that aids in decision-making and decision making?
A decision matrix is a simple but powerful tool for helping managers make decisions. They can think about all options and make informed decisions.
A decision matrix is a way of representing alternatives as rows and columns. This makes it easy for you to see how each option affects other options.
The boxes on the left hand side of this matrix represent four possible choices. Each box represents a different option. The top row depicts the current status quo, while the bottom row represents what would happen if no action was taken.
The middle column displays the impact of selecting Option 1. This would result in an increase of sales of $2 million to $3million.
These are the results of selecting Options 2 or 3. These are both positive changes that increase sales by $1million and $500,000. These changes can also have negative effects. Option 2 increases the cost of goods by $100,000. Option 3 decreases profits and makes them less attractive by $200,000.
The final column shows the results for Option 4. This involves decreasing sales by $1 million.
The best part of using a decision-matrix is that it doesn't require you to know which numbers belong where. You can just glance at the cells and see immediately if one given choice is better.
The matrix has already done all of the work. It is as simple a matter of comparing all the numbers in each cell.
Here is an example of how a decision matrix might be used in your business.
Decide whether you want to invest more in advertising. If you do, you'll be able to increase your revenue by $5 thousand per month. However, this will mean that you'll have additional expenses of $10,000.
The net result of advertising investment can be calculated by looking at the cell below that reads "Advertising." It is 15 thousand. Advertising is a worthwhile investment because it has a higher return than the costs.
Statistics
- The average salary for financial advisors in 2021 is around $60,000 per year, with the top 10% of the profession making more than $111,000 per year. (wgu.edu)
- Your choice in Step 5 may very likely be the same or similar to the alternative you placed at the top of your list at the end of Step 4. (umassd.edu)
- This field is expected to grow about 7% by 2028, a bit faster than the national average for job growth. (wgu.edu)
- The profession is expected to grow 7% by 2028, a bit faster than the national average. (wgu.edu)
- The BLS says that financial services jobs like banking are expected to grow 4% by 2030, about as fast as the national average. (wgu.edu)
External Links
How To
How does Lean Manufacturing work?
Lean Manufacturing uses structured methods to reduce waste, increase efficiency and reduce waste. These processes were created by Toyota Motor Corporation, Japan in the 1980s. The main goal was to produce products at lower costs while maintaining quality. Lean manufacturing focuses on eliminating unnecessary steps and activities from the production process. It consists of five basic elements: pull systems, continuous improvement, just-in-time, kaizen (continuous change), and 5S. Pull systems allow customers to get exactly what they want without having to do extra work. Continuous improvement refers to continuously improving existing processes. Just-in time refers to components and materials being delivered right at the place they are needed. Kaizen means continuous improvement. Kaizen involves making small changes and improving continuously. The 5S acronym stands for sort in order, shine standardize and maintain. These five elements work together to produce the best results.
Lean Production System
Six key concepts underlie the lean production system.
-
Flow is about moving material and information as near as customers can.
-
Value stream mapping is the ability to divide a process into smaller tasks, and then create a flowchart that shows the entire process.
-
Five S's, Sort, Set in Order, Shine. Standardize. and Sustain.
-
Kanban is a visual system that uses visual cues like stickers, colored tape or stickers to keep track and monitor inventory.
-
Theory of Constraints - Identify bottlenecks in the process, and eliminate them using lean tools such kanban boards.
-
Just-in time - Get components and materials delivered right at the point of usage;
-
Continuous improvement: Make incremental improvements to the process instead of overhauling it completely.